Forming method and tool for composite material C-shaped beam
A technology of composite materials and molding methods, which can be applied to other household appliances, household appliances, household components, etc., can solve the problems of unfavorable manufacturing efficiency and manufacturing accuracy, the impact of C-beam molding quality, easy to produce wrinkles, and bending, etc., to achieve Improve the curing effect, simplify the molding difficulty, and improve the molding quality
- Summary
- Abstract
- Description
- Claims
- Application Information
AI Technical Summary
Problems solved by technology
Method used
Image
Examples
Embodiment Construction
[0038] The technical solutions of the present invention will be further described below in conjunction with the accompanying drawings and through specific implementation methods.
[0039] This embodiment provides a method for forming a composite C-beam. By using this forming method, the composite material plate 1 can be made into a C-beam required on aircraft and other equipment. The C-beam has a "C"-shaped structure as a whole. It includes a top plate and two side plates protruding from both ends of the top plate. Specifically, such as figure 1 As shown, the molding method specifically includes the following steps:
[0040] S1. Positioning the composite material plate 1 on the forming surface of the preforming tooling 2, performing thermal diaphragm preforming on the composite material plate 1 to form a C-shaped blank;
[0041] S2. Remove the cover plate 3 at the end of the preforming tooling 2, so that the internal cavity 201 of the preforming tooling 2 communicates with t...
PUM
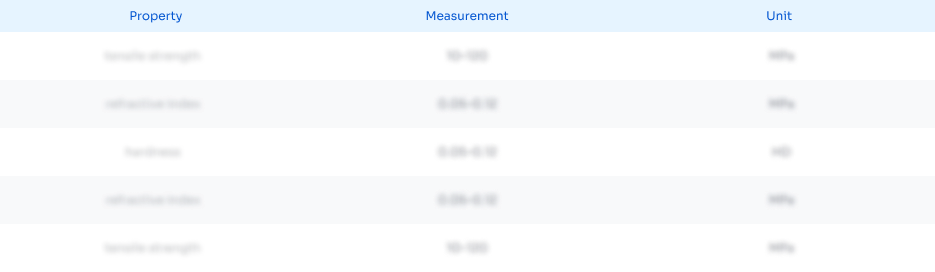
Abstract
Description
Claims
Application Information

- R&D Engineer
- R&D Manager
- IP Professional
- Industry Leading Data Capabilities
- Powerful AI technology
- Patent DNA Extraction
Browse by: Latest US Patents, China's latest patents, Technical Efficacy Thesaurus, Application Domain, Technology Topic, Popular Technical Reports.
© 2024 PatSnap. All rights reserved.Legal|Privacy policy|Modern Slavery Act Transparency Statement|Sitemap|About US| Contact US: help@patsnap.com