A device for improving the stiffness of large wind turbine blades
A wind turbine blade and large-scale technology, applied in the field of wind engineering, can solve problems such as potential safety hazards, difficulty in applying wind environment and earthquake effects, and affecting the service life of the wind turbine system
- Summary
- Abstract
- Description
- Claims
- Application Information
AI Technical Summary
Problems solved by technology
Method used
Image
Examples
Embodiment Construction
[0018] Embodiments of the present invention will be further described in detail below in conjunction with the accompanying drawings.
[0019] The device for improving the stiffness of a large-scale wind turbine blade in this embodiment includes a blade displacement monitoring system 1 installed on a large wind turbine blade 4, a blade stress monitoring system 2, and a stiffness performance adjustment system 3, and the blade displacement monitoring system 1 includes The transmitting end 11, the receiving end 12, the computing integrated module 13 and the imaging surface 14, the transmitting end 11, the receiving end 12 and the imaging surface 14 are all fixed on the tip of the large wind turbine blade 4, and the transmitting end 11 can emit laser signals to the imaging surface 14 , the imaging surface 14 can reflect the laser signal, and the receiving end 12 is facing the imaging surface 14 for receiving the laser signal. There is a certain distance between the receiving end 12 ...
PUM
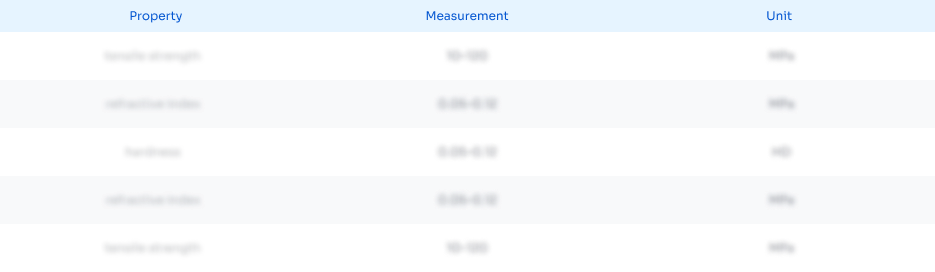
Abstract
Description
Claims
Application Information

- R&D Engineer
- R&D Manager
- IP Professional
- Industry Leading Data Capabilities
- Powerful AI technology
- Patent DNA Extraction
Browse by: Latest US Patents, China's latest patents, Technical Efficacy Thesaurus, Application Domain, Technology Topic, Popular Technical Reports.
© 2024 PatSnap. All rights reserved.Legal|Privacy policy|Modern Slavery Act Transparency Statement|Sitemap|About US| Contact US: help@patsnap.com