Multi-stage excitation double-cylinder magnetorheological damper and control method thereof
A magnetorheological damper, dual-tube technology, applied in the direction of shock absorber, shock absorber, liquid shock absorber, etc., to achieve the effect of expanding the range of controllable damping force
- Summary
- Abstract
- Description
- Claims
- Application Information
AI Technical Summary
Problems solved by technology
Method used
Image
Examples
Embodiment 1
[0032] In view of the limitation that the current magneto-rheological damper can only control the damping force by changing the magnitude of the current under a specific flow gap, this embodiment provides a multi-stage excitation double-tube magnetorheological damper, including a base 2 and an inner tube 7 , an outer cylinder 10, a guide seal assembly, a piston assembly and a magnetic circuit assembly.
[0033] The openings at both ends of the outer cylinder 10 are sealed by a guide sealing assembly and a base 2 respectively. The inner cylinder 7 is coaxially arranged in the outer cylinder 10 . Both ends of the inner cylinder 7 are open against the guide seal assembly and the base 2 respectively. A channel cavity is formed between the outer wall of the inner cylinder 7 and the inner wall of the outer cylinder 10 . A plurality of circulation windows I 701 are opened on the side wall of the inner cylinder 7 close to the end of the guide seal assembly, and a plurality of circul...
Embodiment 2
[0039] The main structure of this embodiment is the same as that of Embodiment 1, wherein, the guide seal assembly includes a guide seat 12 , an oil seal 13 and a pressure plate 14 . One end of the guide seat 12 is in contact with the inner cylinder 7 , and the other end is in contact with the oil seal 13 . An O-ring is arranged on the outer periphery of the guide seat 12 to seal the outer circular surface, and the inner circular surface is sealed by the lip of the oil seal 13 .
Embodiment 3
[0041] The main structure of this embodiment is the same as that of Embodiment 1, wherein, the base 2 has N threaded holes. Injection molded terminals 1 are arranged in the threaded holes. The excitation circuit of each coil 5 is drawn out of the base 2 through the lead wire 3 and the injection molding terminal 1 .
PUM
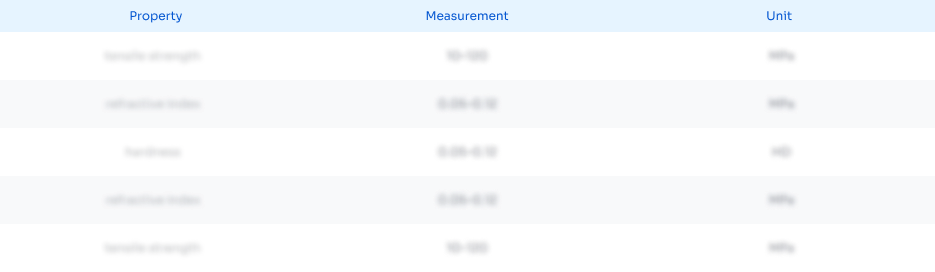
Abstract
Description
Claims
Application Information

- R&D
- Intellectual Property
- Life Sciences
- Materials
- Tech Scout
- Unparalleled Data Quality
- Higher Quality Content
- 60% Fewer Hallucinations
Browse by: Latest US Patents, China's latest patents, Technical Efficacy Thesaurus, Application Domain, Technology Topic, Popular Technical Reports.
© 2025 PatSnap. All rights reserved.Legal|Privacy policy|Modern Slavery Act Transparency Statement|Sitemap|About US| Contact US: help@patsnap.com