Machining clamp for aluminum alloy control arm
A control arm, aluminum alloy technology, applied in the direction of manufacturing tools, metal processing equipment, metal processing mechanical parts, etc., can solve the problem that the three-time clamping cannot meet the accuracy requirements, the structure and shape are complex, and the accuracy requirements are high, and the rotation is light and fast. High production efficiency and stable processing dimensions
- Summary
- Abstract
- Description
- Claims
- Application Information
AI Technical Summary
Problems solved by technology
Method used
Image
Examples
Embodiment 1
[0041] Embodiment 1: The underframe 1 of the processing fixture is fixedly connected to the four-axis bridge plate,
[0042] a. Adjust a pair of positioning pins 9 on a pair of limiting platforms 7 so that the distance they pass through reaches the specified standard;
[0043] B, the positioning sleeve 8 is taken out, and the workpiece is placed, and the vertical hole of the workpiece is inserted into the positioning column 6. At this time, the workpiece falls on the placement platform 71 of one of the four support columns 5 and a pair of limiting platforms 7. At this time A pair of positioning pins 9 on a pair of limiting tables 7 initially limit the workpiece;
[0044] C. The positioning sleeve 8 is inserted into the positioning column 6, and the outer circle of the positioning column is used as the center to adjust the position of the vertical hole so that it is centered, and the centering is adjusted;
[0045] D. After step C is completed, start the pneumatic gripper 3 an...
PUM
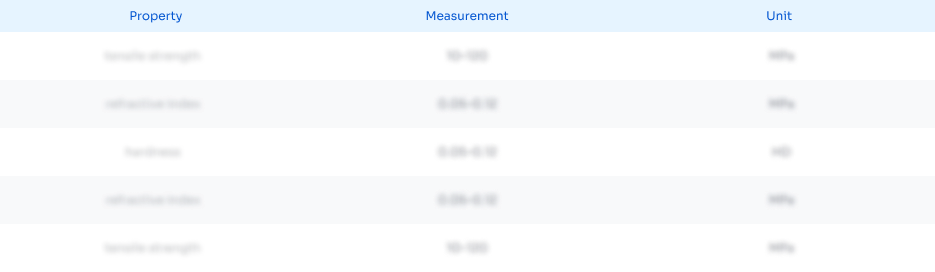
Abstract
Description
Claims
Application Information

- R&D
- Intellectual Property
- Life Sciences
- Materials
- Tech Scout
- Unparalleled Data Quality
- Higher Quality Content
- 60% Fewer Hallucinations
Browse by: Latest US Patents, China's latest patents, Technical Efficacy Thesaurus, Application Domain, Technology Topic, Popular Technical Reports.
© 2025 PatSnap. All rights reserved.Legal|Privacy policy|Modern Slavery Act Transparency Statement|Sitemap|About US| Contact US: help@patsnap.com