Self-sealing gas incoming and release valve
A technology for exhaust valves and intake valves, applied in the direction of cleaning methods using gas flow, valve details, multi-way valves, etc., can solve problems such as incomplete fit, short life of seals, and leakage of explosive gases, and achieve Saving use and maintenance costs, good sealing reliability, and enhanced safety effects
- Summary
- Abstract
- Description
- Claims
- Application Information
AI Technical Summary
Problems solved by technology
Method used
Image
Examples
Embodiment 1
[0017] The technical solution of the present invention will be further described in detail below in conjunction with the accompanying drawings.
[0018] The self-sealing gas intake and exhaust valve is mainly composed of an intake valve body 2 and a working valve body 21. The air intake valve body and the working valve body are a sealed and detachable structure. The intake valve body includes a gas valve core 4 and an oxygen valve. Core 13, exhaust valve core 14 and the clamp 3 of each valve core, and the supporting valve seat 5 and seal 12 of each valve core, one end of the valve core is connected to the suppressor 51 provided by the inverted conical round table, and each clamps The device provides the working power of the clamp through the external power source 1, and the valve core movement hole 22 for the valve core to move in and out is arranged in the intake valve body, and the valve core movement hole divides the intake valve body into an intake working chamber 31 and a ...
PUM
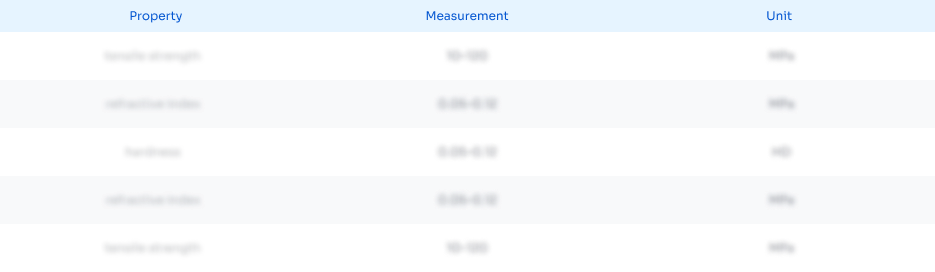
Abstract
Description
Claims
Application Information

- R&D
- Intellectual Property
- Life Sciences
- Materials
- Tech Scout
- Unparalleled Data Quality
- Higher Quality Content
- 60% Fewer Hallucinations
Browse by: Latest US Patents, China's latest patents, Technical Efficacy Thesaurus, Application Domain, Technology Topic, Popular Technical Reports.
© 2025 PatSnap. All rights reserved.Legal|Privacy policy|Modern Slavery Act Transparency Statement|Sitemap|About US| Contact US: help@patsnap.com