Steel member cylinder fitting algorithm
A technology for cylinders and steel members, applied in the field of cylinder fitting algorithms for steel members, can solve the problems of inability to accurately evaluate the construction quality, cumbersome operations, and many uncertain factors.
- Summary
- Abstract
- Description
- Claims
- Application Information
AI Technical Summary
Problems solved by technology
Method used
Image
Examples
Embodiment Construction
[0113] In order to make the purpose, technical solution and advantages of the present invention clearer, the embodiments of the present invention will be further described below in conjunction with the accompanying drawings.
[0114] Please refer to figure 1 , the invention provides a steel member cylinder fitting algorithm, comprising the following steps:
[0115] Step 1: Set multiple measuring points on the cross-section circle to be measured, and arrange high-precision laser instruments to collect the three-dimensional coordinates of the measuring points; connect the high-precision laser instruments to the computer, and transmit the measured data to the computer for processing and calculation in real time.
[0116] Step 2: Use the transfer station algorithm, including orthogonal matrix method, singular value decomposition method, unit quaternion method, and dual quaternion method, to convert the three-dimensional coordinates measured at different measurement positions into ...
PUM
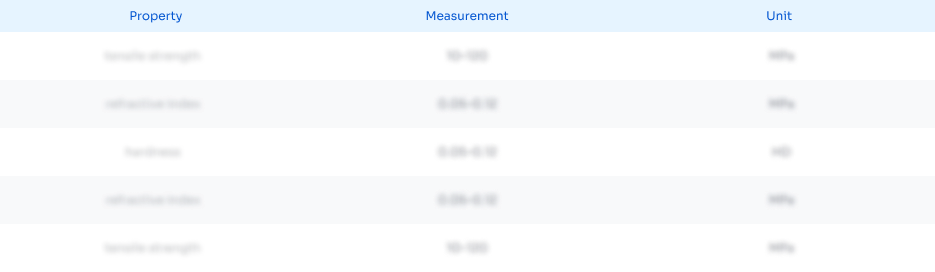
Abstract
Description
Claims
Application Information

- Generate Ideas
- Intellectual Property
- Life Sciences
- Materials
- Tech Scout
- Unparalleled Data Quality
- Higher Quality Content
- 60% Fewer Hallucinations
Browse by: Latest US Patents, China's latest patents, Technical Efficacy Thesaurus, Application Domain, Technology Topic, Popular Technical Reports.
© 2025 PatSnap. All rights reserved.Legal|Privacy policy|Modern Slavery Act Transparency Statement|Sitemap|About US| Contact US: help@patsnap.com