Manufacturing method of subway vehicle chassis
A manufacturing method and chassis technology, which is applied to the chassis, manufacturing tools, railway car body parts, etc., can solve the problems of long manufacturing cycle and low product quality, and achieve the effect of saving operating time and improving assembly
- Summary
- Abstract
- Description
- Claims
- Application Information
AI Technical Summary
Problems solved by technology
Method used
Image
Examples
Embodiment 1
[0035] like Figure 10-13 As shown, the manufacturing process of the subway car underframe in this embodiment, wherein the parts to be assembled include: floor profile one 1, floor profile two 2, floor profile three 3, floor profile four 4, floor profile five 5, bottom profile The frame side beam I6, the bottom frame side beam II7, the traction pillow 9 and the bottom frame end beam 11 mainly include the following steps:
[0036] like Figure 10 As shown, step 1: firstly position the frame side beam I6, and base on the frame side beam I6, and sequentially place floor profile one 1, floor profile two 2, floor profile three 3, floor profile four 4, and floor profile five 5 Assemble, and then assemble the underframe side beam II7 with the outermost floor profile 55, and then weld the welds on both sides of the floor profile 33 in the middle, and finally take these two welds as the benchmark Weld the remaining welds outward to obtain the prefabricated underframe 10;
[0037] St...
Embodiment 2
[0046] Compared with the first embodiment, the manufacturing process of the subway vehicle underframe in this embodiment is only different in that: the floor profile and the side beam of the underframe in the first step are assembled by overlapping.
[0047] In the manufacturing method of the subway vehicle chassis according to the embodiment of the present invention, the two side chassis side beams are adjusted to the automatic welding tire position of the floor profile for overall assembly, and such chassis side beams are connected with the adjacent single floor profile The plug-in assembly is much less difficult than the assembly of the side beams of the bottom frame and the overall floor components; a total of four welds on the front and back sides of the side beams of the bottom frame are manually welded on the bottom frame assembly welding tool, and adjusted From the overall assembly and automatic welding on the floor welding tool, the welding operation efficiency has bee...
PUM
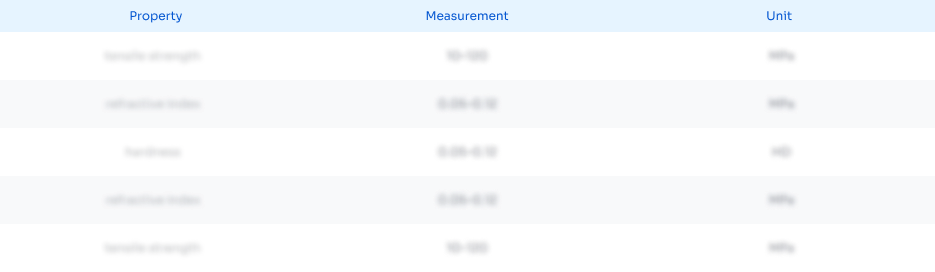
Abstract
Description
Claims
Application Information

- Generate Ideas
- Intellectual Property
- Life Sciences
- Materials
- Tech Scout
- Unparalleled Data Quality
- Higher Quality Content
- 60% Fewer Hallucinations
Browse by: Latest US Patents, China's latest patents, Technical Efficacy Thesaurus, Application Domain, Technology Topic, Popular Technical Reports.
© 2025 PatSnap. All rights reserved.Legal|Privacy policy|Modern Slavery Act Transparency Statement|Sitemap|About US| Contact US: help@patsnap.com