Catalyst for catalytic hydrodechlorination, and preparation method and application thereof
A catalytic hydrogenation and catalyst technology, which is applied in the field of preparation of hydrodechlorination catalysts, can solve the problems of poor catalyst stability, low conversion rate, and short service life, and achieve the effects of good stability, low cost, and high selectivity
- Summary
- Abstract
- Description
- Claims
- Application Information
AI Technical Summary
Problems solved by technology
Method used
Image
Examples
Embodiment 1
[0038] Preparation of Ru-Ni-Li / AC Catalyst
[0039] Configure a certain amount of RuCl 3 ·3H 2 O and NiCl 2 ·6H 2 O mixed solution, the mass fractions were 5.0wt% and 10.0wt%, followed by equal volume impregnation of the pretreated activated carbon, and dried at 90°C for 6h. The dried catalyst precursor was placed in a tube furnace, fed with He gas, the temperature was raised to 320 °C at a rate of 5 °C / min, calcined for 8 h, and then naturally cooled to room temperature to form a Ru-Ni / AC catalyst precursor. An equal volume of 5.2 wt% LiCl solution was impregnated into the Ru-Ni / AC catalyst precursor and dried at 60 °C for 8 h. The dried material was placed in a tube furnace, fed with Ar gas, the temperature was raised to 420°C at a rate of 5°C / min, calcined for 9h, and then naturally cooled to room temperature. The obtained catalyst was Ru-Ni-Li / AC catalyst.
Embodiment 2
[0041] Preparation of Ru-Ti-Pt-Sm / AC Catalyst
[0042] Configure a certain amount of RuCl 3 ·3H 2 O, TiCl 4 and PtCl 2 Mix the solution, the mass fractions are 3.6wt%, 9.6wt% and 1.3wt%, then impregnate the pretreated activated carbon with equal volume, and dry at 105°C for 12h. The dried catalyst precursor was put into a tube furnace, fed with He gas, the temperature was raised to 500°C at 5°C / min, calcined for 7h, and then naturally cooled to room temperature to form a Ru-Ti-Pt / AC catalyst precursor . 0.8wt% SmCl 3 An equal volume of the solution was impregnated into the Ru-Ti-Pt / AC catalyst precursor, and dried at 75 °C for 10 h. The dried material was placed in a tube furnace and fed with N 2 Gas, the temperature was raised to 480°C at 5°C / min, calcined for 13 hours, and then naturally cooled to room temperature. The obtained catalyst was Ru-Ti-Pt-Sm / AC catalyst.
Embodiment 3
[0044] Preparation of Ru-Co-Cs-Sc Catalyst
[0045] Configure a certain amount of RuCl 3 ·3H 2 O and Co(NO3) 2 ·6H 2 O mixed solution, the mass fractions were 2.7wt% and 8.4wt%, followed by an equal volume impregnation of the pretreated activated carbon, and dried at 110 °C for 11 h. The dried catalyst precursor was placed in a tube furnace and fed with N 2 / He mixed gas, the temperature was raised to 385 °C at 5 °C / min, calcined for 16 h, and then naturally cooled to room temperature to form a Ru-Co / AC catalyst precursor. 2.8wt% CsNO3 and 9.8wt% ScCl 3 An equal volume of the mixed solution was impregnated into the Ru-Ni / AC catalyst precursor, and dried at 95 °C for 16 h. Put the dried material into a tube furnace, feed Ar gas, raise the temperature to 360°C at 5°C / min, calcinate for 7h, and then naturally cool to room temperature. The obtained catalyst is Ru-Co-Cs-Sc / AC catalyst .
PUM
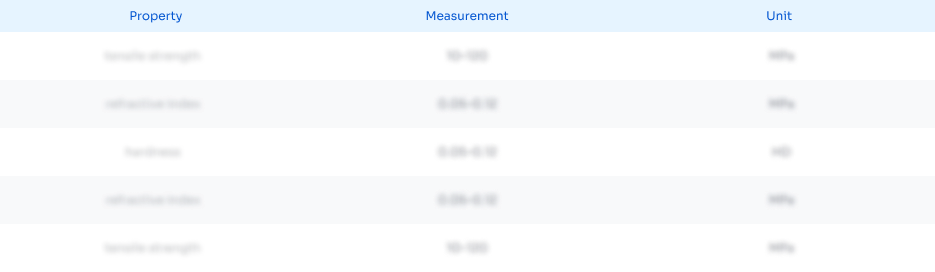
Abstract
Description
Claims
Application Information

- R&D
- Intellectual Property
- Life Sciences
- Materials
- Tech Scout
- Unparalleled Data Quality
- Higher Quality Content
- 60% Fewer Hallucinations
Browse by: Latest US Patents, China's latest patents, Technical Efficacy Thesaurus, Application Domain, Technology Topic, Popular Technical Reports.
© 2025 PatSnap. All rights reserved.Legal|Privacy policy|Modern Slavery Act Transparency Statement|Sitemap|About US| Contact US: help@patsnap.com