Composite airfoil sandwich structure and forming method thereof
A sandwich structure and composite material technology, which is applied in other household appliances, household appliances, household components, etc., to achieve the effect of satisfying structural strength design, ensuring consistency, and ensuring compliance
- Summary
- Abstract
- Description
- Claims
- Application Information
AI Technical Summary
Problems solved by technology
Method used
Image
Examples
Embodiment 1
[0058] Forming a composite material wing "sandwich" weight-reducing structure includes the following steps:
[0059] ①Set the density to 110kg / m 3 The Degussa PMI foam is tested for compressive strength, and the compressive strength of the foam is required to be not less than 1.9MPa at 130°C, and it can be used only after passing the test.
[0060] ②Machining the qualified foam figure 1 shape.
[0061] ③Put the foam in wing root zone Ⅰ according to figure 2 The shape of the foam is pre-cut into three pieces; after drying the machine-added foam in an oven at 130°C±5°C for 3 hours, use a hair dryer to clean the surface debris.
[0062] ④Apply a layer of J-47B glue evenly on the surface of the foam, let it dry for 20-30 minutes, and stick a layer of J-47A glue film.
[0063] ⑤Wrap each of the three pieces of pre-cut foam in wing root area Ⅰ with 4 layers of carbon fiber prepreg (T700 / 9368 prepreg), lay up [90 / 90 / 0 / 90], and then combine the three pieces of foam with Ⅱ ~ The ...
PUM
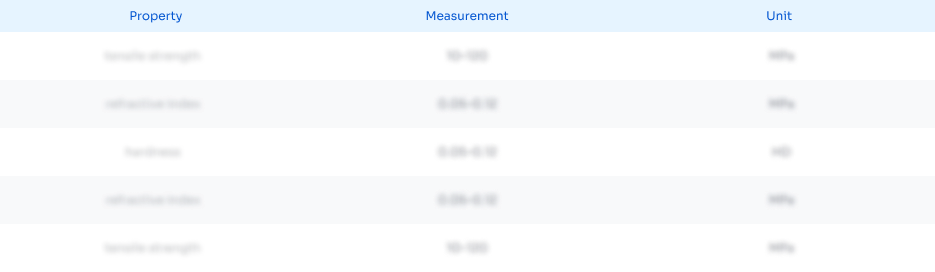
Abstract
Description
Claims
Application Information

- Generate Ideas
- Intellectual Property
- Life Sciences
- Materials
- Tech Scout
- Unparalleled Data Quality
- Higher Quality Content
- 60% Fewer Hallucinations
Browse by: Latest US Patents, China's latest patents, Technical Efficacy Thesaurus, Application Domain, Technology Topic, Popular Technical Reports.
© 2025 PatSnap. All rights reserved.Legal|Privacy policy|Modern Slavery Act Transparency Statement|Sitemap|About US| Contact US: help@patsnap.com