Two-step oxidation synthesized water electrolysis anode and preparation method thereof
A technology for oxidative synthesis and electrolysis of water, applied in electrodes, electrolysis processes, electrolysis components, etc., can solve the problems of industrial production difficulties, high energy consumption of oxygen evolution electrodes, etc., and achieve the effects of low cost, simple preparation method, and rich sources of raw materials
- Summary
- Abstract
- Description
- Claims
- Application Information
AI Technical Summary
Problems solved by technology
Method used
Image
Examples
Embodiment 1
[0029] Embodiment 1: the present invention provides a kind of technical scheme:
[0030] In-Situ Chemical Oxidation Electrolyzed Water Anode with Metallic Nickel Mesh
[0031] Step A: Surface treatment of metal nickel mesh
[0032] Put the cut metal-based electrode into acetone and ethanol solution for ultrasonic cleaning for 5-20 minutes to remove the grease layer on the metal surface; then place the bottom of the metal nickel mesh electrode in a hydrochloric acid solution with a concentration of 0.5-6 moles per liter for ultrasonic cleaning 5 to 20 minutes, then rinse with deionized water to remove the oxide layer on the metal surface;
[0033] Step B: Chemical Oxidation of Metallic Nickel Mesh
[0034] Put the metal nickel mesh after cleaning into the mixed solution of ammonium thiosulfate containing 50 millimoles per liter and 1 mole per liter of hydrochloric acid at normal temperature, and let it stand for 3 hours;
[0035] Three-electrode test of oxygen evolution perf...
Embodiment 2
[0039] Embodiment 2: the present invention provides a kind of technical scheme:
[0040] Two-step Oxidation Electrolyzed Water Anode with Metallic Nickel Mesh
[0041] Step A: Surface treatment of metal nickel mesh
[0042] Put the cut metal-based electrode into acetone and ethanol solution for ultrasonic cleaning for 5-20 minutes to remove the grease layer on the metal surface; then put the metal nickel mesh electrode into the hydrochloric acid solution with a concentration of 0.5-6 moles per liter and ultrasonically clean it for 5 minutes. ~20 minutes, then rinse with deionized water to remove the oxide layer on the metal surface;
[0043] Step B: Chemical Oxidation of Metallic Nickel Mesh
[0044] Put the metal nickel mesh after cleaning into the mixed solution of ammonium thiosulfate containing 50 millimoles per liter and 1 mole per liter of hydrochloric acid at normal temperature, and let it stand for 3 hours;
[0045] Step C: Electrochemical anodization of metallic ni...
Embodiment 3
[0051] Embodiment 3: the present invention provides a kind of technical scheme:
[0052] Step A: Surface treatment of metallic nickel foam
[0053] Put the cut metal foam nickel electrode into acetone and ethanol solution for ultrasonic cleaning for 5-20 minutes to remove the grease layer on the metal surface; then place the metal foam nickel electrode in a hydrochloric acid solution with a concentration of 0.5-6 moles per liter for ultrasonic cleaning 5 to 20 minutes, then rinse with deionized water to remove the oxide layer on the metal surface;
[0054] Step B: Chemical Oxidation of Metallic Nickel Foam
[0055] Put the metal foam nickel after cleaning into the hydrochloric acid mixed solution containing 50 millimoles per liter of ammonium thiosulfate and 1 mole per liter of hydrochloric acid at normal temperature, and let it stand for 3 hours;
[0056] Step C: Electrochemical anodization of metallic nickel foam
[0057] The metal foamed nickel obtained in step B is used...
PUM
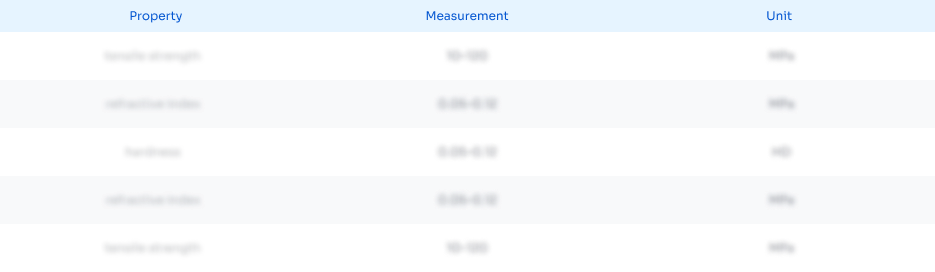
Abstract
Description
Claims
Application Information

- R&D Engineer
- R&D Manager
- IP Professional
- Industry Leading Data Capabilities
- Powerful AI technology
- Patent DNA Extraction
Browse by: Latest US Patents, China's latest patents, Technical Efficacy Thesaurus, Application Domain, Technology Topic, Popular Technical Reports.
© 2024 PatSnap. All rights reserved.Legal|Privacy policy|Modern Slavery Act Transparency Statement|Sitemap|About US| Contact US: help@patsnap.com