Robot workstation for feeding and discharging iron base plates in space between polishing process and sand blasting process
A robot and workstation technology, applied to used abrasive processing devices, grinding/polishing equipment, abrasives, etc., can solve problems such as labor-intensive, impacted product quality, workpiece bumps, etc., to ensure safety, avoid Bump and surface scratches, convenient clamping effect
- Summary
- Abstract
- Description
- Claims
- Application Information
AI Technical Summary
Problems solved by technology
Method used
Image
Examples
Embodiment
[0026] like Figure 1 to Figure 9 As shown, this embodiment provides a robot workstation for loading and unloading iron soleplates between polishing and sandblasting, which includes a robot 3; the driving end of the robot 3 is fixed with a mounting beam 302; the mounting beam 302 The bottom side is equipped with at least one second rotating mechanism 303 for 90-degree rotation of the soleplate 8 of the iron; the rotating end of the bottom side of the second rotating mechanism 303 is equipped with a clamping mechanism 304; A clamping block 305 is installed on the clamping end; the inner side of the clamping block 305 is provided with a clamping groove 306 for clamping the edge of the soleplate of the iron; .
[0027] In the robot workstation of this embodiment for loading and unloading iron soleplates between polishing and sandblasting, the robot 3 is a six-axis robot.
[0028] In a robot workstation of the present embodiment, which is used for loading and unloading iron sole...
PUM
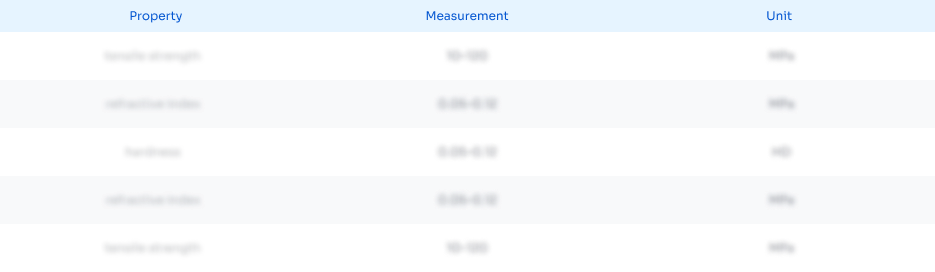
Abstract
Description
Claims
Application Information

- R&D
- Intellectual Property
- Life Sciences
- Materials
- Tech Scout
- Unparalleled Data Quality
- Higher Quality Content
- 60% Fewer Hallucinations
Browse by: Latest US Patents, China's latest patents, Technical Efficacy Thesaurus, Application Domain, Technology Topic, Popular Technical Reports.
© 2025 PatSnap. All rights reserved.Legal|Privacy policy|Modern Slavery Act Transparency Statement|Sitemap|About US| Contact US: help@patsnap.com