Bearing roller pin size detection system and method based on machine vision
A technology of machine vision and size detection, applied in sorting and other directions, can solve the problems of slow scanning speed, high price, unsuitable for large-scale applications, etc., and achieve good robustness
- Summary
- Abstract
- Description
- Claims
- Application Information
AI Technical Summary
Problems solved by technology
Method used
Image
Examples
Embodiment 1
[0112] A bearing needle roller size detection system based on machine vision, including a steel structure support for supporting, a transmission mechanism is provided on the steel structure support, the transmission mechanism includes a drive motor fixed on the steel structure support, the drive motor The output shaft is connected with a motor controller, the motor controller controls the output speed, and is coaxially connected with the transmission wheel with the transmission structure. After the transmission wheel is driven, the conveyor belt tensioned on the two transmission wheels can be driven.
[0113] In order to accommodate workpieces to be inspected, grooves for accommodating workpieces to be inspected, such as needle rollers, are provided on the conveyor belt. In this embodiment, the conveyor belt is made of transparent material.
[0114] There is a sensor above the conveyor belt, which can use sound-activated sensor, temperature sensor, sunlight sensor, and other s...
Embodiment 2
[0120] A method for detecting the size of bearing needle rollers based on machine vision, comprising the following steps:
PUM
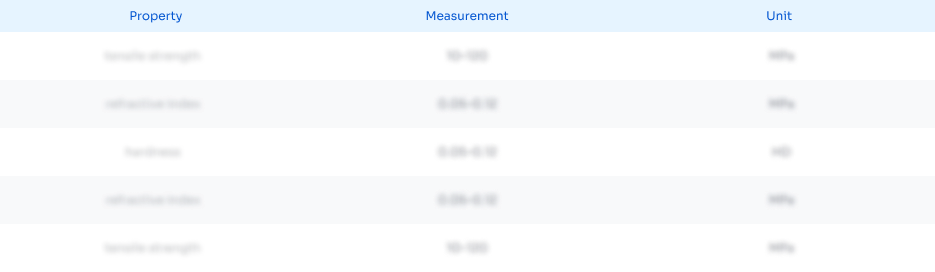
Abstract
Description
Claims
Application Information

- R&D
- Intellectual Property
- Life Sciences
- Materials
- Tech Scout
- Unparalleled Data Quality
- Higher Quality Content
- 60% Fewer Hallucinations
Browse by: Latest US Patents, China's latest patents, Technical Efficacy Thesaurus, Application Domain, Technology Topic, Popular Technical Reports.
© 2025 PatSnap. All rights reserved.Legal|Privacy policy|Modern Slavery Act Transparency Statement|Sitemap|About US| Contact US: help@patsnap.com