Cutoff mechanism for carbon fiber tape feeder
A cutting mechanism, carbon fiber technology, applied in the cutting of textile materials, textiles and papermaking, etc., can solve the problems of insufficient air supply and continuous cutting of carbon fiber material, and achieve the effect of high efficiency
- Summary
- Abstract
- Description
- Claims
- Application Information
AI Technical Summary
Problems solved by technology
Method used
Image
Examples
Embodiment Construction
[0020] In order to make the technical means, creative features, goals and effects achieved by the present invention easy to understand, the present invention will be further elaborated below in conjunction with illustrations and specific embodiments.
[0021] Such as Figure 1 to Figure 4 As shown, a cutting mechanism for carbon fiber strips proposed by the present invention includes a chassis and a base plate 2 fixed on the chassis; a cutter base plate 3 is fixed on the base plate 2, and a fixed Seat 4, the upper side of the fixed seat 4 is provided with an upper knife seat 5, and the lower side of the upper knife seat 5 is fixed with two guide posts 6, and the two guide posts 6 are located on both sides of the fixed seat 4; Two guide posts 6 extend downward into the cabinet 1, and two guide sleeves 7 are fixed on the cutter bottom plate 3, and the two guide sleeves 7 are sleeved on the outside of the guide post 6; the two guide posts The lower end of 6 is fixed with a beari...
PUM
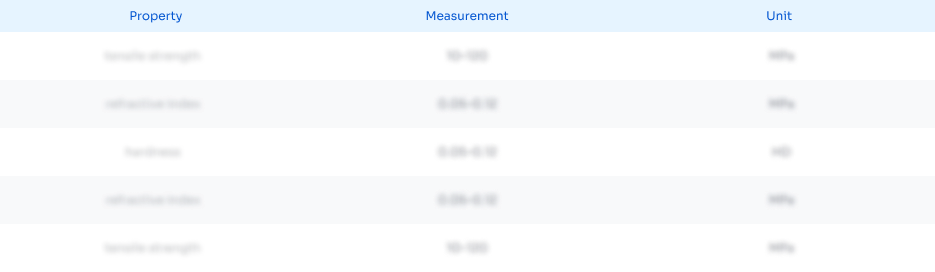
Abstract
Description
Claims
Application Information

- R&D
- Intellectual Property
- Life Sciences
- Materials
- Tech Scout
- Unparalleled Data Quality
- Higher Quality Content
- 60% Fewer Hallucinations
Browse by: Latest US Patents, China's latest patents, Technical Efficacy Thesaurus, Application Domain, Technology Topic, Popular Technical Reports.
© 2025 PatSnap. All rights reserved.Legal|Privacy policy|Modern Slavery Act Transparency Statement|Sitemap|About US| Contact US: help@patsnap.com