Impurity removing and purifying method of sintering machine head dust lixivium
A technology of leaching liquid and head ash, which is applied in the field of impurity removal and purification of sintering head ash leachate, which can solve the problems of no sintering ash leachate purification and impurity removal, and the influence of potassium chloride product purity, achieving good impurity removal effect and filtration steps The effect of less, high purity
- Summary
- Abstract
- Description
- Claims
- Application Information
AI Technical Summary
Problems solved by technology
Method used
Image
Examples
Embodiment 1
[0031] A method for removing impurities and purifying a sintering machine head ash leachate, comprising the following steps:
[0032] a. Take the sintering head ash of four electric fields and soak in water, the water-cement mass ratio is 8:1, and the leach solution obtained by solid-liquid separation is 1L; the main components of the above four electric field sintering head ash are: iron 20.31%, potassium chloride 34.87%, chlorine Sodium chloride 3.53%, zinc 0.05%, lead 1.85%, magnesium oxide 0.80%, sulfur 7.66%, copper 0.11%, calcium oxide 6.27%, silicon dioxide 3.05%, aluminum oxide 2.86%, other ingredients 18.64%.
[0033]b. First add 0.31g of Na to the leaching solution 2 S·9H 2 O solid, stir 2min with the rotating speed of 300r / min;
[0034] c. Add 4.02g of anhydrous K 2 CO 3 Solid, stirred at a speed of 400r / min for 7min;
[0035] d. Finally add 20.08g of BaCl 2 2H 2 0, stirred at a speed of 500r / min for 12min;
[0036] e. vacuum filter the turbid leach solution...
Embodiment 2
[0038] A method for removing impurities and purifying a sintering machine head ash leachate, comprising the following steps:
[0039] a. Take the sintering head ash of the three electric fields and soak in water, the water-cement mass ratio is 6:1, and the leachate obtained by solid-liquid separation is 1L; the main components of the above three electric field sintering head ash are: iron 29.62%, potassium chloride 22.98%, chlorine Sodium chloride 2.34%, zinc 0.04%, lead 1.23%, magnesium oxide 1.23%, sulfur 4.94%, copper 0.08%; calcium oxide 8.25%, silicon dioxide 3.66%, aluminum oxide 2.27%, other ingredients 23.36%.
[0040] b. First add 0.21g of Na to the leaching solution 2 S·9H 2 O solid, stir 2min with the rotating speed of 200r / min;
[0041] c. Add 3.02g of anhydrous K 2 CO 3 Solid, stirred at a speed of 300r / min for 6min;
[0042] d. Finally add 15.15g of BaCl 2 2H 2 O, stirred for 11min at a speed of 400r / min;
[0043] e. vacuum filter the turbid leach solutio...
Embodiment 3
[0045] A method for removing impurities and purifying a sintering machine head ash leachate, comprising the following steps:
[0046] a. Take the sintering head ash of two electric fields and soak in water, the water-cement mass ratio is 4:1, and the leaching solution obtained by solid-liquid separation is 1L; the above-mentioned two electric field sintering head ash main components: iron 37.88%, potassium chloride 12.87%, chlorine Sodium chloride 1.32%, zinc 0.02%, lead 0.63%, magnesium oxide 1.55%, sulfur 3.04%, copper 0.05%; calcium oxide 9.66%, silicon dioxide 4.97%, aluminum oxide 1.69%, other ingredients 26.32%.
[0047] b. First add 0.32g of Na to the leaching solution 2 S·9H 2 O solid, stir 2min with the rotating speed of 300r / min;
[0048] b. Then add 4.33g of anhydrous K 2 CO 3 Solid, stirred at a speed of 400r / min for 7min;
[0049] c. Finally add 20.23g of BaCl 2 2H 2 0, stirred at a speed of 500r / min for 12min;
[0050] d. vacuum filter the turbid leaching...
PUM
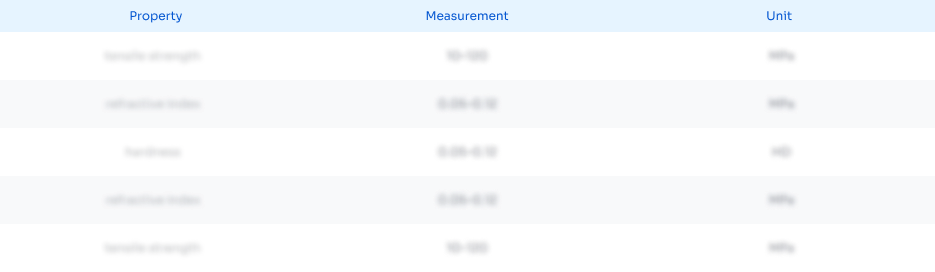
Abstract
Description
Claims
Application Information

- Generate Ideas
- Intellectual Property
- Life Sciences
- Materials
- Tech Scout
- Unparalleled Data Quality
- Higher Quality Content
- 60% Fewer Hallucinations
Browse by: Latest US Patents, China's latest patents, Technical Efficacy Thesaurus, Application Domain, Technology Topic, Popular Technical Reports.
© 2025 PatSnap. All rights reserved.Legal|Privacy policy|Modern Slavery Act Transparency Statement|Sitemap|About US| Contact US: help@patsnap.com