Method for producing oil-field drag reducing agent
A drag reducer and oilfield technology, which is applied in the direction of chemical instruments and methods, drilling compositions, etc., can solve the problems of inefficient use of drag reducer, high price, and insignificant drag reduction effect
- Summary
- Abstract
- Description
- Claims
- Application Information
AI Technical Summary
Problems solved by technology
Method used
Image
Examples
Embodiment 1
[0035] Step 1: After cleaning the reactor with distilled water, let the reactor stand until the inner surface is dry;
[0036] Step 2: Take a certain amount of 300 parts of distilled water and 100 parts of silicone in the main ingredient and put them into the reaction kettle, then add 30 parts of polyethylene oxide, 30 parts of acrylamide, 100 parts of sulfonate, modified 35 parts of permanent acrylic acid, 200 parts of polyisobutylene, 5 parts of polyimide, 50 parts of sodium alkylsulfonate, 10 parts of allyl resin, and 20 parts of amino resin are heated and mixed uniformly, and then coagulated to obtain a paste polymer;
[0037] Step 3: Pass inert gas into the reactor to maintain the current temperature;
[0038] Step 4: Slowly raise the temperature to 150°C, then gradually add 20 parts of pressure-sensitive adhesive, 10 parts of curing agent, 25 parts of monoalkyl phosphate, 18 parts of polyvinyl acetate, 60 parts of isopropanol, 75 parts of benzyl alcohol, poly 60 parts ...
Embodiment 2
[0041] Step 1: After cleaning the reactor with distilled water, let the reactor stand until the inner surface is dry;
[0042] Step 2: Take a certain amount of 400 parts of distilled water and 110 parts of silicone in the main ingredient and put them into the reaction kettle, then add 35 parts of polyethylene oxide, 40 parts of acrylamide, 130 parts of sulfonate, modified 45 parts of non-reactive acrylic acid, 210 parts of polyisobutylene, 7 parts of polyimide, 60 parts of secondary alkyl sodium sulfonate, 20 parts of allyl resin, 30 parts of amino resin, heated and mixed uniformly, and then coagulated to obtain a paste polymer;
[0043] Step 3: Pass inert gas into the reactor to maintain the current temperature;
[0044] Step 4: Slowly raise the temperature to 150°C, then gradually add 25 parts of pressure-sensitive adhesive, 18 parts of curing agent, 22 parts of monoalkyl phosphate, 20 parts of polyvinyl acetate, 70 parts of isopropanol, 85 parts of benzyl alcohol, poly 70 p...
Embodiment 3
[0047] Step 1: After cleaning the reactor with distilled water, let the reactor stand until the inner surface is dry;
[0048] Step 2: Take a certain amount of 500 parts of distilled water and 120 parts of silicone in the main ingredient and put them into the reaction kettle, then add 40 parts of polyethylene oxide, 50 parts of acrylamide, 150 parts of sulfonate, modified 55 parts of non-reactive acrylic acid, 220 parts of polyisobutylene, 9 parts of polyimide, 70 parts of sodium alkyl sulfonate, 30 parts of allyl resin, 35 parts of amino resin, heated and mixed uniformly, and then coagulated to obtain a paste polymer;
[0049] Step 3: Pass inert gas into the reactor to maintain the current temperature;
[0050] Step 4: Slowly raise the temperature to 150°C, then gradually add 30 parts of pressure-sensitive adhesive, 20 parts of curing agent,
[0051] 25 parts of mono-alkyl phosphate, 25 parts of polyvinyl acetate, 80 parts of isopropanol, 95 parts of benzyl alcohol, 80 part...
PUM
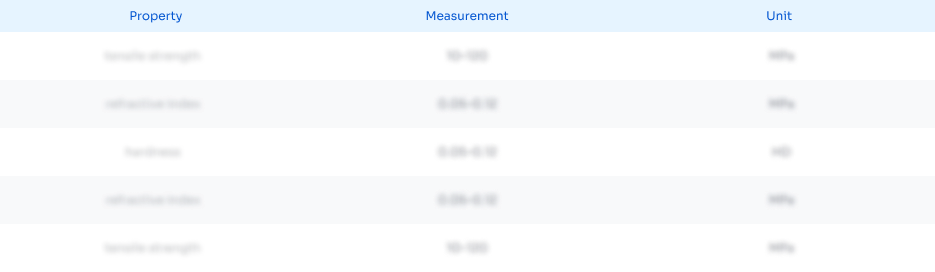
Abstract
Description
Claims
Application Information

- R&D
- Intellectual Property
- Life Sciences
- Materials
- Tech Scout
- Unparalleled Data Quality
- Higher Quality Content
- 60% Fewer Hallucinations
Browse by: Latest US Patents, China's latest patents, Technical Efficacy Thesaurus, Application Domain, Technology Topic, Popular Technical Reports.
© 2025 PatSnap. All rights reserved.Legal|Privacy policy|Modern Slavery Act Transparency Statement|Sitemap|About US| Contact US: help@patsnap.com