Preparation method of cobalt oxide-modified carbon-doped tin-manganese composite oxide nanofibers
A composite oxide and nanofiber technology, applied in the field of material chemistry, can solve the problems of insufficient cycle times and unsatisfactory charge-discharge curves, reducing volume expansion effect, improving electrochemical performance, improving electrical conductivity and cycle performance. Effect
- Summary
- Abstract
- Description
- Claims
- Application Information
AI Technical Summary
Problems solved by technology
Method used
Image
Examples
Embodiment 1
[0029] Weigh 1.0mmol (0.245g) of manganese acetate tetrahydrate (Mn(CH 3 COO) 2 4H 2 O), 1.0mmol (0.351g) dibutyltin oxalate (C 12 h 24 o 4 Sn) was dissolved in 10mL of N,N-dimethylformamide (DMF), then 2.0g of PAN (polyacrylonitrile) was added and stirred for 5h to obtain a light yellow mixture solution precursor; the above light yellow mixture The solution precursor was electrospun at a voltage of 17kV, a flow rate of 0.8mL / h, and an atmosphere with a relative humidity of 30%; the electrospun product obtained above was dried at 120°C;
[0030] Weigh 1.0mmol (0.096g) of 1,2-dimethylimidazole and dissolve it in 10mL of methanol to make solution A; weigh 1.0mmol (0.249g) of cobalt acetate tetrahydrate and dissolve it in 10mL of methanol to make a solution B;
[0031] The dried electrospun product obtained above was soaked in a solution containing Co 2+ Take it out after 30 minutes in methanol solution B containing ions, then take it out after soaking in methanol solution...
Embodiment 2
[0034] Weigh 1.0mmol (0.245g) of manganese acetate tetrahydrate (Mn(CH 3 COO) 2 4H 2 O), 1.0mmol (0.351g) dibutyltin oxalate (C 12 h 24 o 4 Sn) was dissolved in 10mL of N,N-dimethylformamide (DMF), then 2.0g of PAN (polyacrylonitrile) was added and stirred for 5h to obtain a light yellow mixture solution precursor; the above light yellow mixture The solution precursor was electrospun at a voltage of 19kV, a flow rate of 1.0mL / h, and an atmosphere with a relative humidity of 45%; the electrospun product obtained above was dried at 120°C;
[0035] Weigh 1.0mmol (0.096g) of 1,2-dimethylimidazole and dissolve it in 10mL of methanol to make solution A; weigh 2.0mmol (0.498g) of cobalt acetate tetrahydrate and dissolve it in 10mL of methanol to make a solution B;
[0036] The dried electrospun product obtained above was soaked in a solution containing Co 2+ Take it out after 30 minutes in methanol solution B containing ions, then take it out after soaking in methanol solution...
Embodiment 3
[0038] Weigh 1.0mmol (0.245g) of manganese acetate tetrahydrate (Mn(CH 3 COO) 2· 4H 2 O), 1.0mmol (0.351g) dibutyltin oxalate (C 12 h 24 o 4 Sn) was dissolved in 10mL of N,N-dimethylformamide (DMF), then 2.0g of PAN (polyacrylonitrile) was added and stirred for 5h to obtain a light yellow mixture solution precursor; the above light yellow mixture The solution precursor was electrospun at a voltage of 18kV, a flow rate of 0.9mL / h, and an atmosphere with a relative humidity of 40%; the electrospun product obtained above was dried at 120°C;
[0039] Weigh 1.0mmol (0.096g) of 1,2-dimethylimidazole and dissolve it in 10mL of methanol to make solution A; weigh 3.0mmol (0.747g) of cobalt acetate tetrahydrate and dissolve it in 10mL of methanol to make a solution B;
[0040] The dried electrospun product obtained above was soaked in a solution containing Co 2+ Take it out after 30 minutes in methanol solution B containing ions, then take it out after soaking in methanol solutio...
PUM
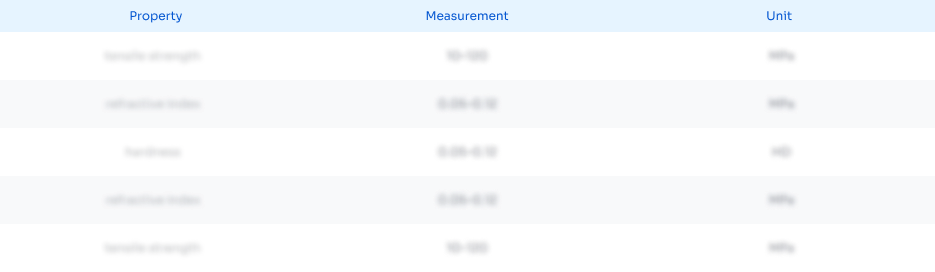
Abstract
Description
Claims
Application Information

- R&D
- Intellectual Property
- Life Sciences
- Materials
- Tech Scout
- Unparalleled Data Quality
- Higher Quality Content
- 60% Fewer Hallucinations
Browse by: Latest US Patents, China's latest patents, Technical Efficacy Thesaurus, Application Domain, Technology Topic, Popular Technical Reports.
© 2025 PatSnap. All rights reserved.Legal|Privacy policy|Modern Slavery Act Transparency Statement|Sitemap|About US| Contact US: help@patsnap.com