Method and production system for continuous catalytic synthesis and separation of high-purity low-viscosity dimethyl silicone oil
A technology of dimethicone and dodecamethylpentasiloxane is applied in the field of continuous catalytic synthesis and separation of high-purity and low-viscosity dimethicone, and can solve the problems that the product cannot be used, the dimethicone is not separated, and the like, Achieve the effect of improving the level of automation control, the reaction is smooth, efficient and stable, and the raw materials are easily available
- Summary
- Abstract
- Description
- Claims
- Application Information
AI Technical Summary
Problems solved by technology
Method used
Image
Examples
Embodiment 1
[0036] Mix hexamethyldisiloxane (MM) and methylcyclosiloxane (DMC) uniformly at a mass ratio of 3:1, pump the mixture into a fixed-bed reactor, and control the reaction temperature at 40°C to a certain The flow rate passes through a fixed bed equipped with an acidic resin. When the mixture passes through the fixed bed, it is catalyzed and balanced under the action of the acidic resin. The reaction time is controlled by controlling the flow rate of the reactant. The reaction residence time is 10 hours, and octamethyltrisilicon is synthesized. A mixture of low-viscosity simethicone oils such as oxane, decamethyltetrasiloxane, dodecamethylpentasiloxane, and tetradecamethylhexasiloxane, accounting for 29.4%, 15.6%, and 7.3%, respectively %, 3.2%.
Embodiment 2
[0038] Mix hexamethyldisiloxane (MM) and methylcyclosiloxane (DMC) uniformly at a mass ratio of 1:3, pump the mixture into a fixed-bed reactor, and control the reaction temperature at 60°C to a certain The flow rate passes through a fixed bed equipped with an acidic resin. When the mixture passes through the fixed bed, it is catalyzed and balanced under the action of the acidic resin. The reaction time is controlled by controlling the flow rate of the reactant. The reaction residence time is 6 hours, and octamethyl trisilicon is synthesized. A mixture of low-viscosity simethicone oils such as oxane, decamethyltetrasiloxane, dodecamethylpentasiloxane, and tetradecamethylhexasiloxane, accounting for 12.8%, 13.1%, and 12.1%, respectively %, 10.8%.
[0039] Two, fractionation: the reaction mixture synthesized by embodiment 2 is pumped into the separation tower, and the separation step: the separation tower comprises a lowering tower, a first separating tower, a second separating t...
Embodiment 3
[0041] The tower pressure is 5-10KPa, the kettle temperature is 90-95°C, and the reflux ratio is 40L / h, so as to collect low-boilers such as hexamethyldisiloxane and octamethyltrisiloxane for reuse. pump into the first separation tower;
[0042] The pressure of the first separation tower is 5-10KPa, the kettle temperature is 110-115°C, and the reflux ratio is 30L / h. Hexasiloxane 99% are used as finished products, and the bottom part of the tower is pumped into the second separation tower;
[0043] The pressure of the second separation tower is 5-10KPa, the kettle temperature is 125-130°C, and the reflux ratio is 25L / h. Hexasiloxane 99% are used as finished products, and the bottom part of the tower is pumped into the de-elevation tower;
[0044] The pressure of the tower is 5-10KPa, the kettle temperature is 140-150°C, the reflux ratio is 20L / h, and the collection of decamethyltetrasiloxane 99%, the heavy components at the bottom of the tower are returned for reuse.
[0...
PUM
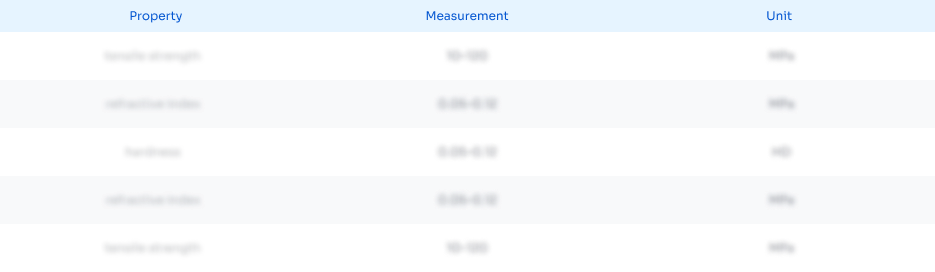
Abstract
Description
Claims
Application Information

- R&D
- Intellectual Property
- Life Sciences
- Materials
- Tech Scout
- Unparalleled Data Quality
- Higher Quality Content
- 60% Fewer Hallucinations
Browse by: Latest US Patents, China's latest patents, Technical Efficacy Thesaurus, Application Domain, Technology Topic, Popular Technical Reports.
© 2025 PatSnap. All rights reserved.Legal|Privacy policy|Modern Slavery Act Transparency Statement|Sitemap|About US| Contact US: help@patsnap.com