Metal stamping part polishing device
A technology of metal stamping parts and grinding mechanism, applied in the field of pressing parts manufacturing, can solve the problems affecting processing accuracy, mold structure, high material requirements, inapplicability, etc., so as to reduce burrs and processing costs, reduce the number of mold sets, improve The effect of production efficiency
- Summary
- Abstract
- Description
- Claims
- Application Information
AI Technical Summary
Problems solved by technology
Method used
Image
Examples
Embodiment Construction
[0023] Combine below Figure 1-9 The present invention is described in detail, and for convenience of description, the orientations mentioned below are now stipulated as follows: figure 1 The up, down, left, right, front and back directions of the projection relationship itself are the same.
[0024] refer to Figure 1-9 , according to an embodiment of the present invention, a grinding device for metal stamping parts includes a housing 10, a feeding chamber 19 is provided through the housing 10 on the left and right, and a lower end is provided in the upper end wall of the feeding chamber 19 to communicate with the feeding chamber. The processing cavity 78 of the cavity 19, the processing cavity 78 is provided with a pressing mechanism 91 for pressing the metal sheet, the upper end wall of the processing cavity 78 is provided with a working cavity 21 with a lower end opening connected to the processing cavity 78, the working cavity A grinding mechanism 90 providing grinding ...
PUM
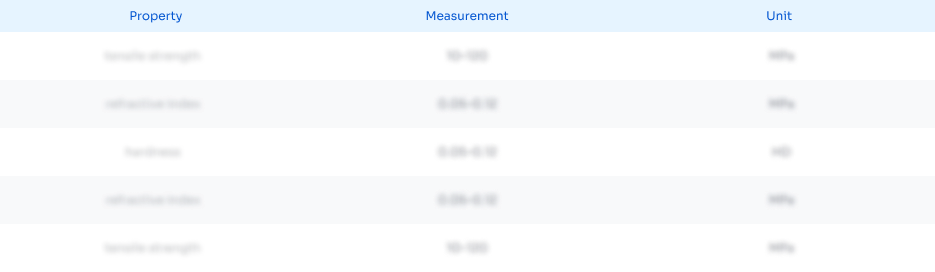
Abstract
Description
Claims
Application Information

- Generate Ideas
- Intellectual Property
- Life Sciences
- Materials
- Tech Scout
- Unparalleled Data Quality
- Higher Quality Content
- 60% Fewer Hallucinations
Browse by: Latest US Patents, China's latest patents, Technical Efficacy Thesaurus, Application Domain, Technology Topic, Popular Technical Reports.
© 2025 PatSnap. All rights reserved.Legal|Privacy policy|Modern Slavery Act Transparency Statement|Sitemap|About US| Contact US: help@patsnap.com