Hardware modular control and drive integrated device
A hardware module, integrated technology, applied in the control system, electrical components, motor control and other directions, can solve the problem of high requirements for trajectory accuracy and speed, affecting the response speed of interpolation points, and limited robot trajectory accuracy and response speed.
- Summary
- Abstract
- Description
- Claims
- Application Information
AI Technical Summary
Problems solved by technology
Method used
Image
Examples
Embodiment 1
[0019] like figure 1 As shown, the hardware modular control-drive integrated device of this embodiment includes a control module 100, a power module 200 and an expansion module 300, and a control-power module interface 400 is provided between the control module 100 and the power module 200, and the control -The power module interface 400 realizes the data exchange between the control module 100 and the power module 200, and the control-expansion module interface 500 is arranged between the control module 100 and the expansion module 300, and the control-expansion module interface 500 realizes the control module 100 and the expansion module The data exchange of module 300; Described control module 100 also comprises non-real-time task processor 110, real-time task processor 120 and FPGA array 130, realizes by shared memory 140 between non-real-time task processor 110 and real-time task processor 120 For data exchange, the non-real-time task processor 110, the real-time task pro...
Embodiment 2
[0021] like figure 1 , 2 As shown, the non-real-time task processor 110 carries application software and performs path planning, and the real-time task processor 120 runs dynamics algorithms, motion planning and interpolation, position closed-loop control, speed closed-loop control, safety system signals and IO signals logic. The FPGA array 130 includes a 1-9 axis motor position acquisition model 131, a 1-9 axis current sampling model 132, a 1-9 axis current closed-loop model 133, a 1-9 axis motor drive signal model 134, and a 1-9 axis temperature sampling model 135 , serial / parallel IO drive model 136 and serial / parallel communication model 137, the serial / parallel IO drive model 136 performs signal interaction with the IO signal logic output by the real-time task processor 120, the 1-9 axis motor drive signal model 134 and the speed closed loop Controls signal interactions. The non-real-time task processor 110 and the real-time task processor 120 run the robot closed-loop...
Embodiment 3
[0023] like figure 1 , 2 As shown, the control-expansion module interface 500 includes a serial / parallel IO signal interface 510 and a serial / parallel communication interface 520, and the expansion module 300 includes a serial / parallel IO drive circuit 310 and a serial / parallel communication circuit 320, and the serial / parallel IO signal interface 510 is respectively connected to the serial / parallel IO driver model 136 and the serial / parallel IO driver circuit 310 , and the serial / parallel communication interface 520 is respectively connected to the serial / parallel communication model 137 and the serial / parallel communication circuit 320 . Control-power module interface 400 includes power system power supply interface 410, safety system signal interface 420, 1-9 axis current sampling interface 430, 1-9 axis drive signal interface 440, 1-9 axis temperature sampling interface 450; 1-9 axis The temperature sampling interface 450 is connected with the 1-9 axis temperature samplin...
PUM
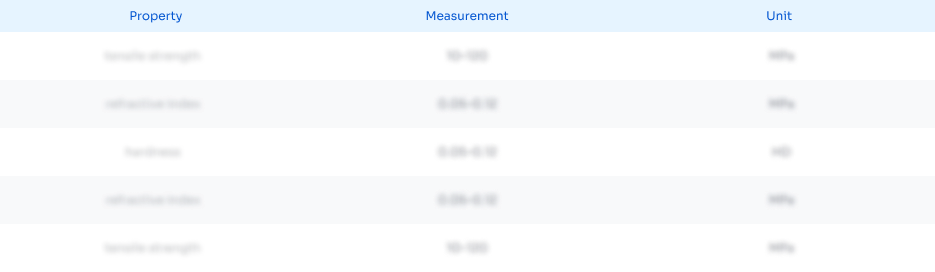
Abstract
Description
Claims
Application Information

- Generate Ideas
- Intellectual Property
- Life Sciences
- Materials
- Tech Scout
- Unparalleled Data Quality
- Higher Quality Content
- 60% Fewer Hallucinations
Browse by: Latest US Patents, China's latest patents, Technical Efficacy Thesaurus, Application Domain, Technology Topic, Popular Technical Reports.
© 2025 PatSnap. All rights reserved.Legal|Privacy policy|Modern Slavery Act Transparency Statement|Sitemap|About US| Contact US: help@patsnap.com