Method for reducing risks of thickened oil emulsification in process of reducing steam huff and puff
A heavy oil and steam technology, which is applied in the direction of earthwork drilling, wellbore/well components, production fluid, etc., can solve the problems that formation emulsification cannot be effectively solved, accelerate heavy oil emulsification, and frequent operation process, so as to reduce heavy oil emulsification Risk, strong operability, effect of improving effect
- Summary
- Abstract
- Description
- Claims
- Application Information
AI Technical Summary
Problems solved by technology
Method used
Image
Examples
example
[0064] Implementation case 1: The third round of huff and puff drainage of well A23H in Lvda 27-2 oilfield in Bohai Sea was not timely resulting in emulsification and poor huff and puff effect.
[0065] Figure 12 It is the location of two steam huff and puff wells in Luda 27-2 oilfield.
[0066] Figure 13(a) shows the daily oil production and water cut curve of Well A23H in Lvda 27-2 Oilfield, which is divided into three stages: the natural energy depletion exploitation stage, the main goal is to determine the production capacity of cold recovery; the first round of steam huff and puff, injection Steam 4500m 3 , the bottom hole injection temperature is 340℃; the second round of steam huff and puff, injecting steam 5250m 3 , Bottom hole injection temperature is 340°C. The viscosity of degassed and dehydrated crude oil in Well A23H at 50°C was 2462mPa·s. After the second round of huff and puff well was opened, the production capacity dropped rapidly. After sampling, the visc...
PUM
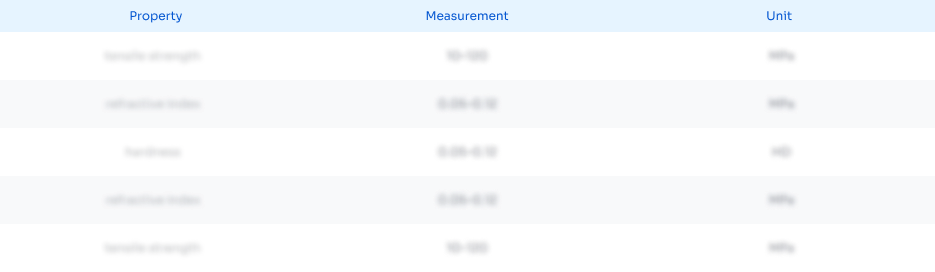
Abstract
Description
Claims
Application Information

- Generate Ideas
- Intellectual Property
- Life Sciences
- Materials
- Tech Scout
- Unparalleled Data Quality
- Higher Quality Content
- 60% Fewer Hallucinations
Browse by: Latest US Patents, China's latest patents, Technical Efficacy Thesaurus, Application Domain, Technology Topic, Popular Technical Reports.
© 2025 PatSnap. All rights reserved.Legal|Privacy policy|Modern Slavery Act Transparency Statement|Sitemap|About US| Contact US: help@patsnap.com