Collaborative robot modularized joint compact in structure
A technology of modular joints and compact structure, which is applied in the direction of manipulators, program-controlled manipulators, manufacturing tools, etc. It can solve the problems of low joint integration, poor modularization, and long design cycle, so as to achieve compact joint structure and increase design flexibility. , The effect of saving axial space
- Summary
- Abstract
- Description
- Claims
- Application Information
AI Technical Summary
Problems solved by technology
Method used
Image
Examples
specific Embodiment approach 1
[0048] Embodiment 1: it includes a joint casing, a drive mechanism, a motor assembly and an output mechanism; the drive mechanism, the motor assembly 15 and the output mechanism are sequentially arranged inside the joint casing, the input end of the motor assembly is connected to the drive mechanism, and the motor assembly 15 The output terminal is connected with the output mechanism.
specific Embodiment approach 2
[0050] The drive mechanism includes a motor end encoder code disc mounting seat 1, a joint servo driver 2, a joint end encoder code disc 3, a joint end encoder reading head 4, a joint end encoder code disc mounting seat 5, a driver bracket 6, Encoder code disc 9 at the motor end, encoder reading head 10 at the motor end, brake assembly 12;
[0051] The motor assembly 15 includes a motor stator, an internal motor rotor and a motor shaft 14;
[0052] The output mechanism includes a harmonic reducer 16, a low-speed wire protection tube 19 and an output flange;
[0053] The joint casing includes a joint housing 13 and a joint rear cover 11;
[0054] The driver bracket 6, the encoder code disc mount 5 at the joint end, the encoder code disc mount 1 at the motor end, the brake assembly 12, the motor assembly 15 and the harmonic reducer 16 are sequentially fixed on the joint housing 13;
[0055] The driver bracket 6 is fixedly connected to the joint housing 13, the joint servo driver...
specific Embodiment approach 3
[0064] Embodiment 3: The inner ring of the brake assembly 12 is provided with a sealing ring mounting seat 7 , and the sealing ring mounting seat 7 is provided with a sealing ring one 8 , and the inner ring of the sealing ring one 8 is in contact with the motor shaft 14 .
[0065] Other implementation manners are the same as the second embodiment.
PUM
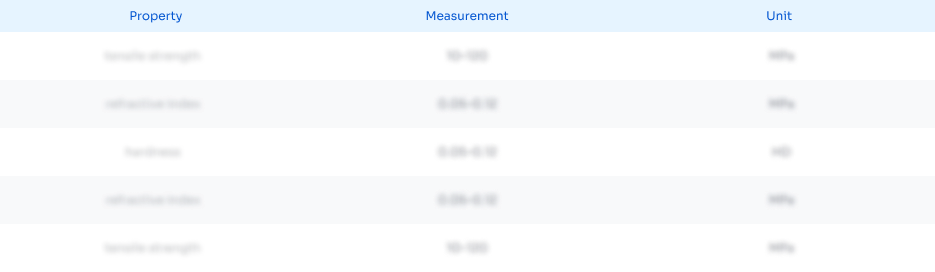
Abstract
Description
Claims
Application Information

- R&D
- Intellectual Property
- Life Sciences
- Materials
- Tech Scout
- Unparalleled Data Quality
- Higher Quality Content
- 60% Fewer Hallucinations
Browse by: Latest US Patents, China's latest patents, Technical Efficacy Thesaurus, Application Domain, Technology Topic, Popular Technical Reports.
© 2025 PatSnap. All rights reserved.Legal|Privacy policy|Modern Slavery Act Transparency Statement|Sitemap|About US| Contact US: help@patsnap.com