A method for recovering carbon, copper and silver in zinc kiln slag
A technology of copper silver and kiln slag, which is applied in the direction of using liquid cleaning methods, cleaning methods and utensils, chemical instruments and methods, etc., can solve the problems of difficult wastewater treatment, large metal loss, high energy consumption, etc., to reduce chemical consumption, The effect of changing the surface activity of minerals and simplifying the process
- Summary
- Abstract
- Description
- Claims
- Application Information
AI Technical Summary
Problems solved by technology
Method used
Image
Examples
Embodiment 1
[0068] The main chemical components of zinc kiln slag raw materials are as follows: Zn 1.88wt%, Cu 1.17wt%, TFe 31.57wt%, S 5.30wt%, total C17.39wt%, Pb 0.25wt%, Ag 298.30g / t; Crush raw zinc kiln slag to -2mm, accounting for 75-80%, and use wet grinding under the condition of pulp weight percentage concentration of 65-70wt%, to -0.074mm, accounting for 80wt%, to obtain flotation raw materials; Put it into the flotation machine for pre-floating carbon. The concentration of the flotation pulp is 25-30wt%, and the flotation stirring speed is 1700rad / min. kerosene 3000g / t, mixed and stirred for 3min, added foaming agent terpineol oil 350g / t, mixed and stirred for 1min, and then inflated and scraped for roughing for 5min to complete pre-floating carbon to obtain carbon rough concentrate and floating carbon tailings, and then Put the coarse carbon concentrate in a flotation machine with a rotating speed of 2300rad / min and mix and stir for 1min, then inflate and concentrate for 3.5mi...
Embodiment 2
[0070] The main chemical components of zinc kiln slag raw materials are as follows: Zn 1.83wt%, Cu 1.14wt%, TFe 31.09wt%, S 5.28wt%, total C18.98wt%, Pb 0.23wt%, Ag 286.12g / t; Crush raw zinc kiln slag to -2mm, accounting for 75-80%, and use wet grinding under the condition of pulp weight percentage concentration of 65-70wt%, to -0.074mm, accounting for 80wt%, to obtain flotation raw materials; Put it into the flotation machine for pre-floating carbon. The concentration of the flotation pulp is 25-30 wt%, and the flotation stirring speed is 1600rad / min. Collecting agent kerosene 3200g / t, mixing and stirring for 3min, adding foaming agent terpineol oil 325g / t, mixing and stirring for 1min, and then inflating and scraping roughing for 5min to complete pre-floating carbon to obtain carbon rough concentrate and floating carbon tailings, Then put the coarse carbon concentrate in a flotation machine with a rotating speed of 2200rad / min and mix and stir for 1min, then inflate and conc...
Embodiment 3
[0072]The main chemical components of zinc kiln slag raw materials are as follows: Zn 1.95wt%, Cu 1.21wt%, TFe 30.31wt%, S 5.41wt%, total C16.26wt%, Pb 0.26wt%, Ag 303.28g / t; Crush raw zinc kiln slag to -2mm, accounting for 75-80%, and use wet grinding under the condition of pulp weight percentage concentration of 65-70wt%, to -0.074mm, accounting for 80wt%, to obtain flotation raw materials; Put it into a flotation machine for pre-floating carbon. The concentration of the flotation pulp is 25-30 wt%, and the stirring speed of the flotation is 1800rad / min. Collecting agent kerosene 2800g / t, mixing and stirring for 3 minutes, adding foaming agent terpineol oil 375g / t, mixing and stirring for 1 minute, and then inflating and scraping and foaming rough separation for 5 minutes to complete pre-floating carbon, and obtain carbon rough concentrate and floating carbon tailings. Then put the coarse carbon concentrate in a flotation machine with a rotating speed of 2400rad / min and mix ...
PUM
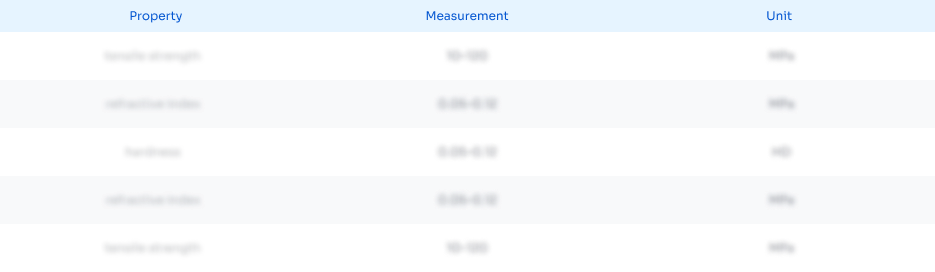
Abstract
Description
Claims
Application Information

- R&D
- Intellectual Property
- Life Sciences
- Materials
- Tech Scout
- Unparalleled Data Quality
- Higher Quality Content
- 60% Fewer Hallucinations
Browse by: Latest US Patents, China's latest patents, Technical Efficacy Thesaurus, Application Domain, Technology Topic, Popular Technical Reports.
© 2025 PatSnap. All rights reserved.Legal|Privacy policy|Modern Slavery Act Transparency Statement|Sitemap|About US| Contact US: help@patsnap.com