Method for solving fracture problem of functionally graded piezoelectric material with any attribute
A piezoelectric material and functional gradient technology, applied in the field of fracture mechanics, can solve the problems of inaccurate crack parameters, limitations, and failure to consider any properties of functional gradient piezoelectric materials, etc., and achieve a wide range of applications.
- Summary
- Abstract
- Description
- Claims
- Application Information
AI Technical Summary
Problems solved by technology
Method used
Image
Examples
specific Embodiment approach 1
[0017] Specific implementation mode one: as figure 1 As shown, a method for solving the fracture problem of a functionally graded piezoelectric material with arbitrary properties described in this embodiment, the method includes the following steps:
[0018] Step 1, establishing the constitutive equation and equilibrium equation of the functionally graded piezoelectric material;
[0019] Step two, such as figure 2 As shown, in order to solve the fracture problem of functionally graded piezoelectric materials with arbitrary properties, for the arbitrariness of the properties of functionally graded piezoelectric materials:
[0020] The functionally graded piezoelectric material is uniformly divided into several layers along the thickness direction, assuming that the material properties of each layer change with the form of exponential function, and the material properties of adjacent layers are continuous at the interface, the constitutive equation and equilibrium established ...
specific Embodiment approach 2
[0026] Specific implementation mode two: the difference between this implementation mode and specific implementation mode one is: the specific process of the step one is:
[0027] For a functionally graded piezoelectric material with a thickness h, the constitutive equation of the functionally graded piezoelectric material is established as:
[0028]
[0029] Where: τ xz Represents the shear stress in the z-axis direction of the functionally graded piezoelectric material on a plane perpendicular to the x-axis, τ yz Represents the z-axis shear stress of the functionally graded piezoelectric material on a plane perpendicular to the y-axis, D x Represents the electrical displacement of the functionally graded piezoelectric material in the x-axis direction, D y Represents the electrical displacement of the functionally graded piezoelectric material in the y-axis direction; the x-axis, y-axis, and z-axis are the three axes of the space Cartesian coordinate system;
[0030] w ...
specific Embodiment approach 3
[0039] Specific implementation mode three: the difference between this implementation mode and specific implementation mode two is: the specific process of said step two is:
[0040] In view of the arbitrariness of the properties of the functionally graded piezoelectric material, in order to solve the material fracture problem, this embodiment adopts a segmented exponential model.
[0041] The functionally graded piezoelectric material is uniformly divided into m layers along the thickness direction, such as image 3 As shown, the thickness of the nth layer of material is h n –h n-1 , where: n=1,2,…,m,h n Represents the sum of thicknesses from the first layer material to the nth layer material, h n-1 Represents the sum of thicknesses from the first layer material to the n-1th layer material;
[0042] The material properties of each layer are assumed to vary exponentially:
[0043]
[0044] c n44Represents the shear modulus of the nth layer material; e n15 Represents ...
PUM
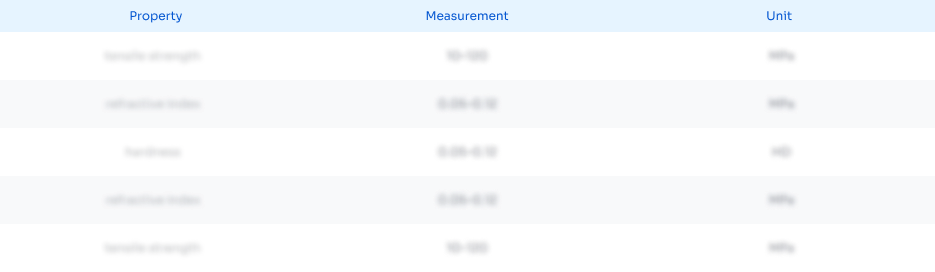
Abstract
Description
Claims
Application Information

- R&D
- Intellectual Property
- Life Sciences
- Materials
- Tech Scout
- Unparalleled Data Quality
- Higher Quality Content
- 60% Fewer Hallucinations
Browse by: Latest US Patents, China's latest patents, Technical Efficacy Thesaurus, Application Domain, Technology Topic, Popular Technical Reports.
© 2025 PatSnap. All rights reserved.Legal|Privacy policy|Modern Slavery Act Transparency Statement|Sitemap|About US| Contact US: help@patsnap.com