Method for making shredded cakes by steam heat treatment of cereals
A production method and technology of finger cakes, which are applied in the field of making finger cakes by steam heat treatment of cereals, can solve the problems of unbalanced nutrition of finger cakes, low utilization rate of grains, high production cost, etc., to meet the dietary value, improve tissue shape, The effect of increasing intestinal peristalsis
- Summary
- Abstract
- Description
- Claims
- Application Information
AI Technical Summary
Problems solved by technology
Method used
Image
Examples
specific Embodiment 1
[0023] (1) Preparation of steam heat-treated oat flour
[0024] The oats with uniform particle size and no deterioration were soaked in distilled water for 3 hours, then put into a steam tank, filled with saturated steam, the pressure was 0.8 MPa, and the pressure was released quickly after 5 minutes of maintenance time. The samples after steam heat treatment are collected, and a vacuum rotary dryer is used to place the dried samples under vacuum conditions and heat and dry in a rotating manner. The water heating temperature is 40 °C, the rotation speed is 3 rpm, and the vacuum degree is 10³Pa. The dried steam-heat-treated grains were milled by combining mechanical pulverization and airflow pulverization. The specific pulverization process was as follows: the dried samples were pulverized by mechanical pulverization, and the feeding rate was 0.1 t / h. The mesh number of the powder is 60 mesh; the coarse powder is pulverized again by jet milling, the feeding speed is 0.5 t / h, t...
specific Embodiment 2
[0029] (1) Preparation of buckwheat flour by steam heat treatment
[0030] Buckwheat with uniform particle size and no deterioration was soaked in distilled water for 3 hours, then put into a steam tank, and filled with saturated steam, the pressure was 0.8 MPa, and the pressure was released quickly after 5 minutes of maintenance time. The samples after steam heat treatment are collected, and a vacuum rotary dryer is used to place the dried samples under vacuum conditions and heat and dry in a rotating manner. The water heating temperature is 40 °C, the rotation speed is 3 rpm, and the vacuum degree is 10³Pa. The dried steam-heat-treated grains were milled by combining mechanical pulverization and airflow pulverization. The specific pulverization process was as follows: the dried samples were pulverized by mechanical pulverization, and the feeding rate was 0.1 t / h. The mesh number of the powder is 60 mesh; the coarse powder is pulverized again by jet milling, the feeding spee...
specific Embodiment 3
[0035] (1) Preparation of steam heat-treated corn flour
[0036] The corn with uniform particle size and no deterioration was soaked in distilled water for 3 hours, then put into a steam tank, and filled with saturated steam, the pressure was 0.8 MPa, and the pressure was released quickly after 5 minutes of maintenance time. The samples after steam heat treatment are collected, and a vacuum rotary dryer is used to place the dried samples under vacuum conditions and heat and dry in a rotating manner. The water heating temperature is 40 °C, the rotation speed is 3 rpm, and the vacuum degree is 10³Pa. The dried steam-heat-treated grains were milled by combining mechanical pulverization and airflow pulverization. The specific pulverization process was as follows: the dried samples were pulverized by mechanical pulverization, and the feeding rate was 0.1 t / h. The mesh number of the powder is 60 mesh; the coarse powder is pulverized again by jet milling, the feeding speed is 0.5 t / ...
PUM
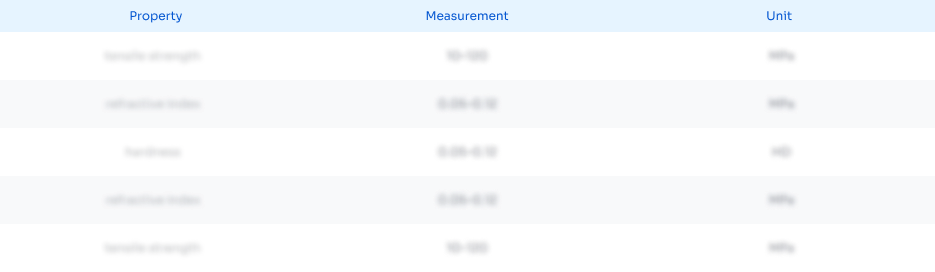
Abstract
Description
Claims
Application Information

- Generate Ideas
- Intellectual Property
- Life Sciences
- Materials
- Tech Scout
- Unparalleled Data Quality
- Higher Quality Content
- 60% Fewer Hallucinations
Browse by: Latest US Patents, China's latest patents, Technical Efficacy Thesaurus, Application Domain, Technology Topic, Popular Technical Reports.
© 2025 PatSnap. All rights reserved.Legal|Privacy policy|Modern Slavery Act Transparency Statement|Sitemap|About US| Contact US: help@patsnap.com