Counter balance flange joint and application thereof
A balance method and reverse technology, which is applied in the directions of wind power generation, wind engine assembly, installation/supporting wind engine configuration, etc. It can solve the problems of large deviation of tower roundness, difficulty in guaranteeing weld quality, and heavy welding workload and other problems, to achieve the effect of reducing the deformation of the tower tube, facilitating mechanical flat welding, and reducing the amount of welding
- Summary
- Abstract
- Description
- Claims
- Application Information
AI Technical Summary
Problems solved by technology
Method used
Image
Examples
Embodiment
[0058] A reverse balanced flange joint, such as figure 1 As shown, the upper flange tower 1 and the lower flange tower 2 are included, and the upper flange tower 1 and the lower flange tower 2 are welded to the tower cylinder body 14. Such as figure 2 Shown and image 3 , The inner wall of the upper flange tower tube 1 is welded with a top stiffening plate 3, the inner wall of the lower flange tower tube 2 is welded with a guiding stiffening plate 4, and the upper surface of the top stiffening plate 3 is connected with an upper flange plate 5 through structural glue to guide the stiffening The lower surface of the plate 4 is connected with the lower flange plate 6 through structural glue, the upper flange plate 5 and the lower flange plate 6 are provided with bolt holes 7, and the high-strength bolt 8 penetrates the upper flange plate 5 and the lower flange through the bolt holes 7 The plate 6 connects the upper flange tower 1 and the lower flange tower 2; the top stiffening pl...
PUM
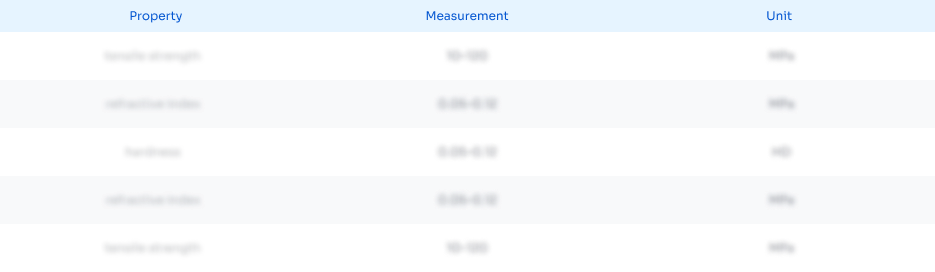
Abstract
Description
Claims
Application Information

- R&D
- Intellectual Property
- Life Sciences
- Materials
- Tech Scout
- Unparalleled Data Quality
- Higher Quality Content
- 60% Fewer Hallucinations
Browse by: Latest US Patents, China's latest patents, Technical Efficacy Thesaurus, Application Domain, Technology Topic, Popular Technical Reports.
© 2025 PatSnap. All rights reserved.Legal|Privacy policy|Modern Slavery Act Transparency Statement|Sitemap|About US| Contact US: help@patsnap.com