Parallel-type three-degree-of-freedom piezoelectric resonance self-actuating mechanism and excitation method thereof
An actuating mechanism, piezoelectric resonance technology, applied in the direction of piezoelectric effect/electrostrictive or magnetostrictive motors, generators/motors, electrical components, etc., can solve the problems of slow speed and small driving force
- Summary
- Abstract
- Description
- Claims
- Application Information
AI Technical Summary
Problems solved by technology
Method used
Image
Examples
specific Embodiment approach 1
[0015] Specific implementation mode 1. Combination Figure 1-Figure 3 To illustrate this specific embodiment, the parallel three-degree-of-freedom piezoelectric resonant self-actuating mechanism described in this embodiment includes four columnar piezoelectric transducers 1, 2, 3 and 4 with identical structures and four shared Connecting beam 5, four driving beams 6,
[0016] The structures of the columnar piezoelectric transducers 1, 2, 3 and 4 are the same, and the columnar piezoelectric transducer 1 is taken as an example for illustration. The components included in the columnar piezoelectric transducer 1 include a Screw 7-1, a terminal column 8-1, a connecting plate 9, two piezoelectric ceramic components 10-1, 10-2, a ground electrode piece 11 and a driving terminal column 12, wherein the connecting plate 9 and the driving terminal column 12 are common parts for four columnar piezoelectric transducers. refer to figure 1 , the four connecting beams 5 are actually the pa...
specific Embodiment approach 2
[0020] Specific Embodiment 2. The difference between this embodiment and the parallel-connected three-degree-of-freedom piezoelectric resonant self-actuating mechanism described in Specific Embodiment 1 is that four phases with a phase difference of π / 2 are provided for the columnar voltage conversion electric energy device. Periodic sinusoidal voltage signal V a , V b , V c , V d , the four-phase voltage signals can be V a =V m sin(ωt), V b =V m sin(ωt+π / 2), V c =V m sin(ωt+π), V d =V m sin(ωt+3π / 2), where V m Indicates the amplitude of the voltage signal, and the frequency ω of the voltage signal is close to or consistent with the first-order longitudinal vibration natural frequency of the cylindrical piezoelectric transducer to be excited.
[0021] In this embodiment, setting the working plane: first set the Cartesian rectangular coordinate system, the three axes are x, y, z respectively, o is the origin of the coordinate system, the xoy plane is selected as the ...
specific Embodiment approach 3
[0025] Embodiment 3. The difference between this embodiment and the parallel three-degree-of-freedom piezoelectric resonant self-actuating mechanism described in Embodiment 1 is that each piezoelectric ceramic sheet is composed of a piezoelectric body and a pair of electrode coatings , the two coatings that make up the pair of electrode coatings are respectively located on the square surfaces on both sides of the piezoelectric body.
[0026] The piezoelectric body described in this embodiment is formed of lead zirconate titanate piezoelectric ceramics, but is not limited to lead zirconate titanate piezoelectric ceramics, and can also be formed of other piezoelectric materials such as polyvinylidene fluoride and aluminum nitride. Piezoelectric body. The electrode coating is realized by coating of appropriate metal materials such as Al, Cu, Ag, Ag-Pd alloy and the like arranged on the surface of the piezoelectric ceramic sheet.
[0027] Specific embodiment four, combine figure...
PUM
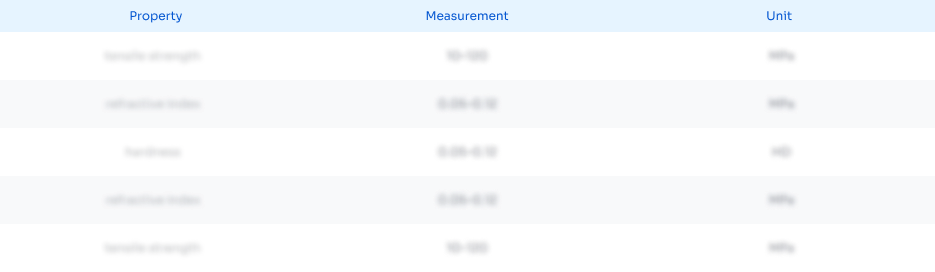
Abstract
Description
Claims
Application Information

- R&D
- Intellectual Property
- Life Sciences
- Materials
- Tech Scout
- Unparalleled Data Quality
- Higher Quality Content
- 60% Fewer Hallucinations
Browse by: Latest US Patents, China's latest patents, Technical Efficacy Thesaurus, Application Domain, Technology Topic, Popular Technical Reports.
© 2025 PatSnap. All rights reserved.Legal|Privacy policy|Modern Slavery Act Transparency Statement|Sitemap|About US| Contact US: help@patsnap.com