Combustion chamber
A combustion chamber and fuel technology, applied in the field of aero-engines, can solve the problems of inability to meet the low pollution requirements of the engine, high CO and UHC emissions, uneven local equivalence ratio, etc., and achieve strong shearing, uniform combustion, and uniform mixing of oil and gas Effect
- Summary
- Abstract
- Description
- Claims
- Application Information
AI Technical Summary
Problems solved by technology
Method used
Image
Examples
Embodiment Construction
[0029] Embodiments of the present invention will now be described in detail with reference to the accompanying drawings.
[0030] The present invention will be further described below in conjunction with the accompanying drawings and specific embodiments.
[0031] figure 1 Shown is the basic structure of an aeroengine applied to the combustor 4 , which includes a fan 1 , a low-pressure compressor 2 , a high-pressure compressor 3 , a combustor 4 , a high-pressure turbine 5 and a low-pressure turbine 6 . When the aero-engine is working, the incoming air flows through the fan 1, and after being compressed by the low-pressure compressor 2, it enters the high-pressure compressor 3, and then the high-pressure air enters the combustion chamber 4 to burn with fuel, and the high-temperature and high-pressure gas formed after combustion enters the The high-pressure turbine 5 and the low-pressure turbine 6 respectively drive the high-pressure compressor 3 , the fan 1 and the low-pressur...
PUM
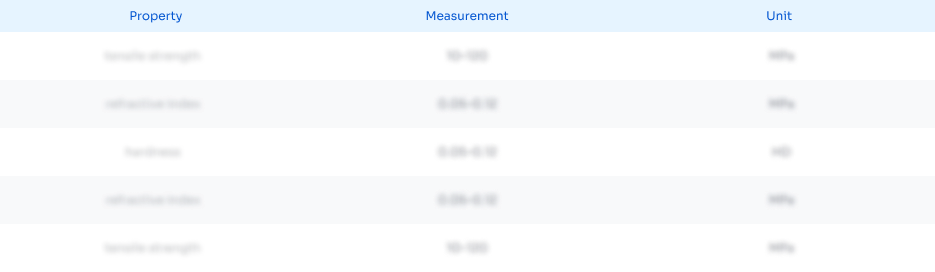
Abstract
Description
Claims
Application Information

- R&D
- Intellectual Property
- Life Sciences
- Materials
- Tech Scout
- Unparalleled Data Quality
- Higher Quality Content
- 60% Fewer Hallucinations
Browse by: Latest US Patents, China's latest patents, Technical Efficacy Thesaurus, Application Domain, Technology Topic, Popular Technical Reports.
© 2025 PatSnap. All rights reserved.Legal|Privacy policy|Modern Slavery Act Transparency Statement|Sitemap|About US| Contact US: help@patsnap.com