Nondestructive testing robot system and method for aircraft skin surface defects
A robotic system, aircraft skin technology, applied in aircraft component testing, optical testing flaws/defects, instruments, etc., can solve the problems of accelerated crack deterioration, manual inspection by technicians, easy loss, error, leakage, etc., to meet the smart effect
- Summary
- Abstract
- Description
- Claims
- Application Information
AI Technical Summary
Problems solved by technology
Method used
Image
Examples
Embodiment Construction
[0045]In order to make the technical problems, technical solutions and beneficial effects to be solved by the present invention clearer, the present invention will be further described in detail below in conjunction with the accompanying drawings and embodiments. It should be understood that the specific embodiments described here are only used to explain the present invention, not to limit the present invention.
[0046] Such as image 3 As shown, in an embodiment provided by the present invention, a robot system for non-destructive testing of aircraft skin surface defects includes a multi-base laser scanning full-space positioning system 10, an AGV trolley 20, a six-degree-of-freedom mechanical arm 30, and a terminal binocular Structured light measurement sensor 40, software system 50; during the detection process of aircraft skin surface defects, global positioning is performed by multi-base laser scanning full-space positioning system 10;
[0047] Such as figure 1 with ...
PUM
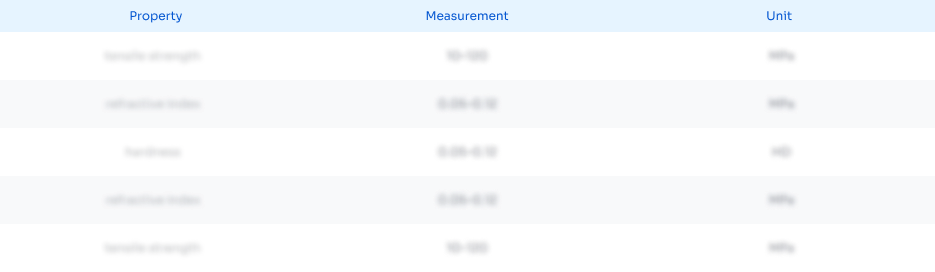
Abstract
Description
Claims
Application Information

- R&D
- Intellectual Property
- Life Sciences
- Materials
- Tech Scout
- Unparalleled Data Quality
- Higher Quality Content
- 60% Fewer Hallucinations
Browse by: Latest US Patents, China's latest patents, Technical Efficacy Thesaurus, Application Domain, Technology Topic, Popular Technical Reports.
© 2025 PatSnap. All rights reserved.Legal|Privacy policy|Modern Slavery Act Transparency Statement|Sitemap|About US| Contact US: help@patsnap.com