Superposed beam connection joint, construction method and superposed beam production process
A technology for connecting nodes and production processes, applied in joists, girders, truss beams, etc., can solve the problems of poor strength of connecting nodes, poor bending resistance of laminated beams, etc., and achieve strong bending resistance, improved performance, and excellent tensile performance. Effect
- Summary
- Abstract
- Description
- Claims
- Application Information
AI Technical Summary
Problems solved by technology
Method used
Image
Examples
Embodiment 2
[0080] This embodiment introduces the second implementation mode. In this mode, the composite beam 002 has the same structure as the above-mentioned composite beam. Refer to Figure 7 , the difference is that a corbel 003 made of concrete is prefabricated on the concrete column 001, and the structure of the corbel is the same as that of the end of the composite beam, that is, a T-shaped groove is provided on the corbel 003, that is, The T-shaped slot is a part of the corbel, and the connecting piece 400 is used between the corbel and the composite beam for quick connection, and the secondary pouring of concrete can also realize the final prefabricated connection.
Embodiment 3
[0082] Further improvement is carried out on the basis of Embodiment 1. Specifically, the steel bar 110 part is curved at the end of the secondary pouring area, that is, a curved structure. This structure is conducive to improving the strength of the steel bar in the secondary pouring area. Pull-out resistance. refer to Figure 13 The structure and style shown in . At the same time, between two adjacent composite beams, the ends of the steel strands are fixed and fastened with U-shaped locks to form an integrated structure.
Embodiment 4
[0084] The above steel bar 11 is replaced by a light steel keel 110'. Specifically, the light steel keel is rolled with a thin steel plate of 1 to 3 mm, and the cross section is a U-shaped channel steel structure, and it is galvanized. The middle part has a curved structure that arches upwards. refer to Figure 14 The style shown in .
[0085] In this embodiment, the bending prestress of the channel steel and the tension prestress of the steel strand are fully utilized.
PUM
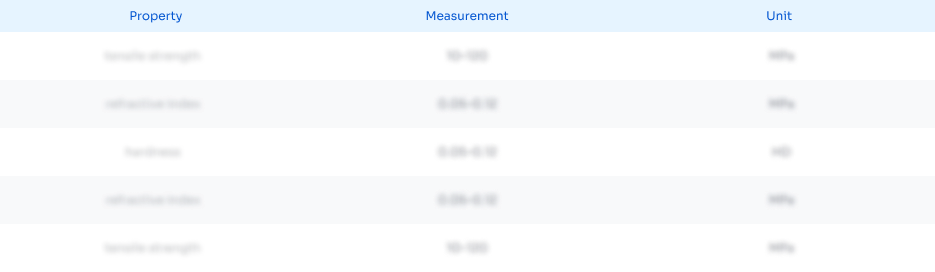
Abstract
Description
Claims
Application Information

- R&D Engineer
- R&D Manager
- IP Professional
- Industry Leading Data Capabilities
- Powerful AI technology
- Patent DNA Extraction
Browse by: Latest US Patents, China's latest patents, Technical Efficacy Thesaurus, Application Domain, Technology Topic, Popular Technical Reports.
© 2024 PatSnap. All rights reserved.Legal|Privacy policy|Modern Slavery Act Transparency Statement|Sitemap|About US| Contact US: help@patsnap.com