Heat exchange process and heat exchange system for ethylene cracking furnace
A technology of ethylene cracking furnace and heat exchange system, which is applied in steam boilers, lighting and heating equipment, steam generation, etc. It can solve the problems of insufficient energy utilization and high energy consumption, reduce condensation and coking, prolong production cycle, and improve energy conversion. The effect of thermal efficiency
- Summary
- Abstract
- Description
- Claims
- Application Information
AI Technical Summary
Problems solved by technology
Method used
Image
Examples
Embodiment 1
[0052] Present embodiment 1 (energy-saving flow process 1), adopts such as Figure 5 The cracking furnace of the ethylene plant is shown. The heat exchange system includes a steam drum 4, a first quench heat exchanger group and a second quench heat exchanger group; Heat exchanger, the second-stage quenching heat exchanger; the second quenching heat exchanger group includes a first-stage quenching heat exchanger, which is a third-stage quenching heat exchanger; the first-stage quenching heat exchanger is a vertical The linear quenching heat exchanger; the second-stage quenching heat exchanger and the third-stage quenching heat exchanger are horizontal shell-and-tube quenching heat exchangers. The boiler feed water preheating section b of the ethylene cracking furnace is divided into an upper boiler feed water preheating section BFW-I and a lower boiler feed water preheating section BFW-II connected thereto; the first stage quenching heat exchanger and the second stage The she...
Embodiment 2
[0064] Present embodiment 2 (energy-saving flow process 2), adopts such as Figure 6 The cracking furnace of the ethylene plant is shown. The difference from Example 1 is that only two stages of rapid cooling heat exchangers are included in the process.
[0065] After the cracked gas comes out of the furnace tube of the radiant section of the cracking furnace, it passes through the first-stage quenching heat exchanger and the second-stage quenching heat exchanger in sequence; wherein, the cracked gas is exchanged with the boiler feed water from the steam drum in the first quenching heat exchanger. Heat exchange, heat exchange with the boiler feed water preheated by the convection section in the second-stage quenching heat exchanger.
[0066] After all the boiler feed water is preheated by the upper boiler feed water preheating section BFW-I, part of the boiler feed water is sent to the second stage quenching heat exchanger to exchange heat with the cracked gas; the other part...
PUM
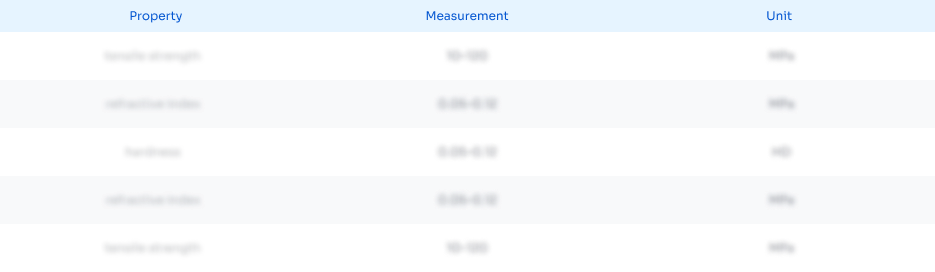
Abstract
Description
Claims
Application Information

- R&D Engineer
- R&D Manager
- IP Professional
- Industry Leading Data Capabilities
- Powerful AI technology
- Patent DNA Extraction
Browse by: Latest US Patents, China's latest patents, Technical Efficacy Thesaurus, Application Domain, Technology Topic, Popular Technical Reports.
© 2024 PatSnap. All rights reserved.Legal|Privacy policy|Modern Slavery Act Transparency Statement|Sitemap|About US| Contact US: help@patsnap.com