Polyurethane-based transparent antifouling coating preparation method
An anti-fouling coating and polyurethane technology, applied in polyurea/polyurethane coatings, anti-fouling/underwater coatings, coatings, etc., can solve the problem of poor anti-fouling properties, poor durability, sacrificing material light transmission, and limiting anti-fouling surfaces, etc. problems, to achieve the effects of high non-toxicity, easy regulation of molecular weight and dosage, and improved durability
- Summary
- Abstract
- Description
- Claims
- Application Information
AI Technical Summary
Problems solved by technology
Method used
Examples
Embodiment 1
[0026] Preparation of acetylated starch: Accurately weigh 5g of amylose and add it to a three-neck flask, add 10.79g of glacial acetic acid, stir for 5 minutes, add 9.45g of acetic anhydride, stir for 15min, add 0.18g of methanesulfonic acid catalyst, and heat at 75°C Under reaction 24h. After the reaction, the reactant was moved into a constant pressure funnel, and slowly added dropwise to the stirring deionized water for washing. After the dropwise addition, vacuum filtration was started and rinsed with deionized water to wash away the acetic acid until neutral. The finally obtained product was dried at 60° C. for 3 h to obtain the product.
[0027] Preparation of polyurethane-based transparent antifouling coating with 0.5wt% PDMS-OH: Accurately weigh 1.05mg polydimethylsiloxane (PDMS-OH) and 50mg hexamethylene diisocyanate trimer (HDIT) into In a 3 mL transparent glass bottle, add 0.5 mL methyl ethyl ketone to shake and dissolve it, and put it in an oven at 75°C for the fi...
Embodiment 2
[0029] Preparation of acetylated starch: Accurately weigh 5g of amylose and add it to a three-neck flask, add 10.79g of glacial acetic acid, stir for 5 minutes, add 9.45g of acetic anhydride, stir for 15min, add 0.18g of methanesulfonic acid catalyst, and heat at 75°C Under reaction 24h. After the reaction, the reactant was moved into a constant pressure funnel, and slowly added dropwise to the stirring deionized water for washing. After the dropwise addition, vacuum filtration was started and rinsed with deionized water to wash away the acetic acid until neutral. The finally obtained product was dried at 60° C. for 3 h to obtain the product.
[0030]Preparation of polyurethane-based transparent antifouling coating with 1wt% PDMS-OH: Accurately weigh 2.10mg of polydimethylsiloxane (PDMS-OH) and 50mg of hexamethylene diisocyanate trimer (HDIT) into 3mL In a transparent glass bottle, add 0.5mL methyl ethyl ketone to shake and dissolve it, and put it in an oven at 75°C for the f...
Embodiment 3
[0032] Preparation of acetylated starch: Accurately weigh 5g of amylose and add it to a three-neck flask, add 10.79g of glacial acetic acid, stir for 5 minutes, add 9.45g of acetic anhydride, stir for 15min, add 0.18g of methanesulfonic acid catalyst, and heat at 75°C Under reaction 24h. After the reaction, the reactant was moved into a constant pressure funnel, and slowly added dropwise to the stirring deionized water for washing. After the dropwise addition, vacuum filtration was started and rinsed with deionized water to wash away the acetic acid until neutral. The finally obtained product was dried at 60° C. for 3 h to obtain the product.
[0033] Preparation of polyurethane-based transparent antifouling coating of 2.5wt% PDMS-OH: Accurately weigh 5.25mg polydimethylsiloxane (PDMS-OH) and 50mg hexamethylene diisocyanate trimer (HDIT) into In a 3 mL transparent glass bottle, add 0.5 mL methyl ethyl ketone to shake and dissolve it, and put it in an oven at 75°C for the firs...
PUM
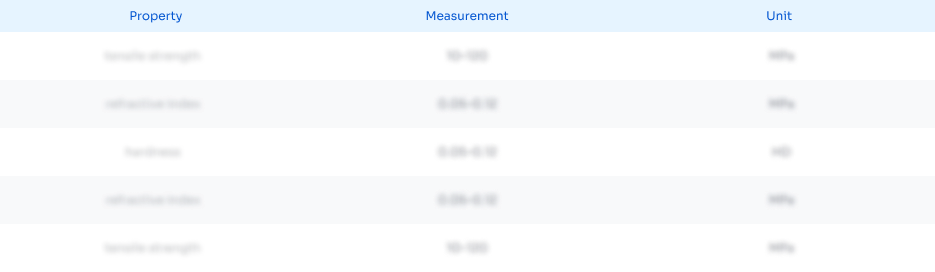
Abstract
Description
Claims
Application Information

- R&D
- Intellectual Property
- Life Sciences
- Materials
- Tech Scout
- Unparalleled Data Quality
- Higher Quality Content
- 60% Fewer Hallucinations
Browse by: Latest US Patents, China's latest patents, Technical Efficacy Thesaurus, Application Domain, Technology Topic, Popular Technical Reports.
© 2025 PatSnap. All rights reserved.Legal|Privacy policy|Modern Slavery Act Transparency Statement|Sitemap|About US| Contact US: help@patsnap.com