Sand core used for sand casting and preparing method thereof
A sand casting and sand core technology, which is applied in the field of hollow sand core preparation of sand casting, can solve the problems of large air volume of the sand core and difficulty in sand falling, and achieve the effects of reducing casting costs, improving quality, and reducing the amount of sand used
- Summary
- Abstract
- Description
- Claims
- Application Information
AI Technical Summary
Problems solved by technology
Method used
Image
Examples
preparation example Construction
[0041] Such as figure 1 Shown, the preparation method of the sand core of the present embodiment comprises the following steps:
[0042] S21. Design of sand core 1: according to the shape of sand core 1, design a three-dimensional model of sand core 1 through modeling software. A sand discharge piston 4 is provided at the sand port 3, and a vent hole 5 is provided on the sand discharge piston 4;
[0043] S2. Sand core 1 preparation: use 3DP resin sand to prepare sand core 1 and sand discharge piston 4 through 3DP printing equipment;
[0044] S3. Filling sand discharge: discharge the dry sand in the cavity 2 through the sand discharge port 3;
[0045] S4. Rubber sealing of the sand discharge port 3: the sand discharge piston 4 is sealed to the sand discharge port 3 with heat-resistant glue.
Embodiment 2
[0047] Such as Figure 4~6 As shown, the present embodiment provides a sand core for sand casting, which includes a sand core 1, a cavity 2 is provided inside the sand core 1, and the sand core 1 is provided with at least one sand outlet 3, so as to figure 2 In the shown embodiment, three sand discharge ports 3 are provided, and a sand discharge piston 4 for blocking the sand discharge ports 3 is provided at the sand discharge ports 3 . In order to ensure that the shape is consistent after plugging, a stop 31 with a large outside and a small inside is provided at the sand discharge port 3, and a boss matching the stop 31 is provided on the end face of the sand discharge piston 4, so that the sand discharge piston 4 is covered to the sand discharge. At the mouth, the outer end face of the sand discharge piston 4 is flush with the end face of the sand discharge port 3. The sand discharge piston 4 is provided with an exhaust hole 5 .
[0048] see Figure 4 , the section of th...
Embodiment 3
[0054] Example 3, see Figure 8 , is a cross-sectional view of a hollow sand core for sand casting. The difference from the previous embodiment is that the hollow grid shape is an equilateral triangle.
[0055] The preparation method of the hollow sand core for sand casting is the same as the method in Example 1. After the filling sand in the grid is emptied, the sand discharge piston is used to block the sand discharge port with heat-resistant glue.
PUM
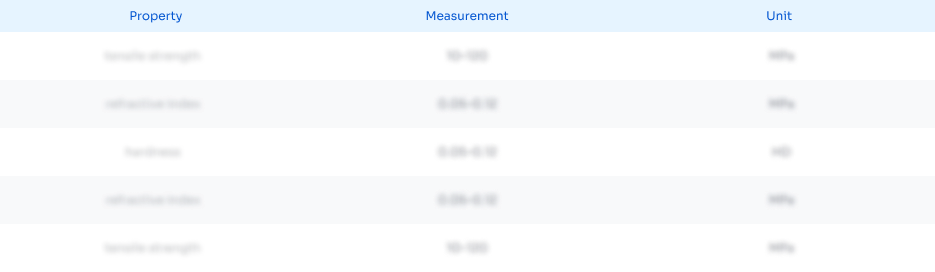
Abstract
Description
Claims
Application Information

- R&D
- Intellectual Property
- Life Sciences
- Materials
- Tech Scout
- Unparalleled Data Quality
- Higher Quality Content
- 60% Fewer Hallucinations
Browse by: Latest US Patents, China's latest patents, Technical Efficacy Thesaurus, Application Domain, Technology Topic, Popular Technical Reports.
© 2025 PatSnap. All rights reserved.Legal|Privacy policy|Modern Slavery Act Transparency Statement|Sitemap|About US| Contact US: help@patsnap.com