Furnace pressure control method and device for annealing furnace
A technology of furnace pressure control and annealing furnace, which is applied in the direction of heat treatment process control, furnace, heat treatment furnace, etc., can solve the problems of influence, inability to effectively guarantee the effect of reduction reaction, waste of protective gas, etc.
- Summary
- Abstract
- Description
- Claims
- Application Information
AI Technical Summary
Problems solved by technology
Method used
Image
Examples
Embodiment 1
[0046] The embodiment of the present invention provides a furnace pressure control method of an annealing furnace. The method is applied to each furnace section of the annealing furnace. Each furnace section is provided with an injection pipe for injecting protective gas. The injection pipe is provided with a flow control device, such as figure 1 As shown, the method includes: S101, obtaining the current furnace pressure value of the annealing furnace; S102, judging whether the furnace pressure value satisfies the preset furnace pressure range; S103, when the preset furnace pressure range is satisfied, based on the furnace pressure value , the flow correction coefficient of the injection pipeline in the target furnace section, the flow rate rating of the injection pipeline, and obtain the flow correction value for correcting the flow controlled by the flow controller on the injection pipeline; S104, based on the flow correction value, the The flow controller performs correctio...
Embodiment 2
[0067] Based on the same inventive concept, the embodiment of the present invention provides an annealing furnace pressure control device, such as figure 2 shown, including:
[0068] Obtaining module 201, obtaining the current furnace pressure value of the annealing furnace;
[0069] A judging module 202, configured to judge whether the furnace pressure value satisfies a preset furnace pressure range;
[0070] The first obtaining module 203 is configured to obtain the value of the furnace pressure based on the furnace pressure value, the flow correction coefficient of the injection pipeline in the target furnace section, and the flow rate rating of the injection pipeline when the preset furnace pressure range is satisfied. A flow correction value for correcting the flow controlled by the flow controller on the injection pipeline;
[0071] A correction control module 204, configured to perform correction control on the flow controller based on the flow correction value.
[...
PUM
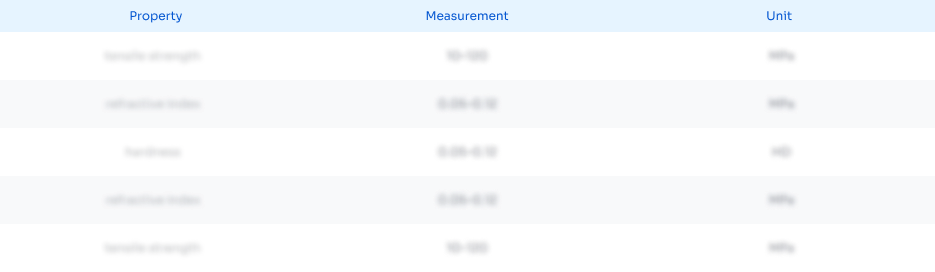
Abstract
Description
Claims
Application Information

- R&D
- Intellectual Property
- Life Sciences
- Materials
- Tech Scout
- Unparalleled Data Quality
- Higher Quality Content
- 60% Fewer Hallucinations
Browse by: Latest US Patents, China's latest patents, Technical Efficacy Thesaurus, Application Domain, Technology Topic, Popular Technical Reports.
© 2025 PatSnap. All rights reserved.Legal|Privacy policy|Modern Slavery Act Transparency Statement|Sitemap|About US| Contact US: help@patsnap.com