Insulation bag processing process and insulation bag processed through process
A processing technology, a technology of thermal insulation packs, applied in thermal insulation containers, packaging, transportation and packaging, etc., can solve the problems of reducing the sealing performance and quality of thermal insulation packs, the seams cannot be well sealed, and affecting the overall appearance of thermal insulation packs, etc. Avoid wire aging and breakage, improve thermal insulation, and avoid deformation
- Summary
- Abstract
- Description
- Claims
- Application Information
AI Technical Summary
Problems solved by technology
Method used
Image
Examples
Embodiment Construction
[0026] The present invention will be further described in detail below in conjunction with specific embodiments and accompanying drawings.
[0027] Please refer to figure 1 and figure 2 , in a preferred embodiment, the thermal insulation bag processing technology of the present invention comprises the following steps:
[0028] S1. Cutting the raw materials to obtain the bag outer body panel 1, the bag inner body panel 2, the inner sleeve mouth panel 3, the inner sleeve bottom panel 4, the bag cover panel 5, and the bag bottom panel 6. In this embodiment, thermoplastic materials are used as raw materials, including TPU (thermoplastic polyurethane elastomer rubber), PVC (polyvinyl chloride), TPU composite fabric, and PVC composite fabric, but not limited thereto.
[0029] S2. The bag outer zipper 7 and the bag inner zipper 8 are respectively welded on the longer side of the bag outer large body panel 1 and the bag inner large body panel 2 by a high frequency welding machine,...
PUM
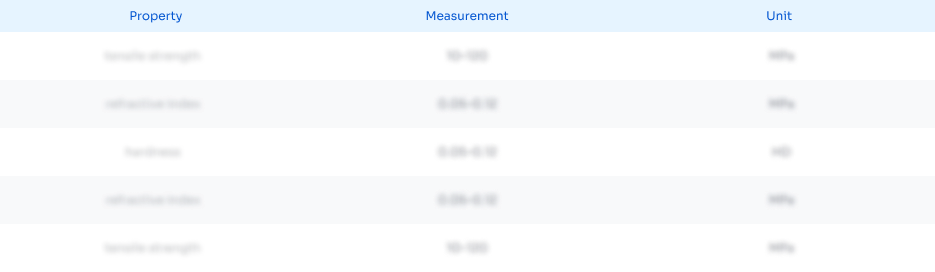
Abstract
Description
Claims
Application Information

- Generate Ideas
- Intellectual Property
- Life Sciences
- Materials
- Tech Scout
- Unparalleled Data Quality
- Higher Quality Content
- 60% Fewer Hallucinations
Browse by: Latest US Patents, China's latest patents, Technical Efficacy Thesaurus, Application Domain, Technology Topic, Popular Technical Reports.
© 2025 PatSnap. All rights reserved.Legal|Privacy policy|Modern Slavery Act Transparency Statement|Sitemap|About US| Contact US: help@patsnap.com