An orthotropic steel bridge deck roof fatigue crack detection system based on ultrasonic guided wave method
An ultrasonic guided wave, orthotropic technology, applied in the analysis of solids using sonic/ultrasonic/infrasonic waves, material analysis using sonic/ultrasonic/infrasonic waves, and measuring devices, etc. question
- Summary
- Abstract
- Description
- Claims
- Application Information
AI Technical Summary
Problems solved by technology
Method used
Image
Examples
specific Embodiment approach 1
[0047] Specific implementation mode one: refer to image 3 Describe this embodiment in detail. A fatigue crack detection system for orthotropic steel bridge deck roof deck based on the ultrasonic guided wave method described in this embodiment includes a detection part and a control part, and the detection part includes: a bracket and a transducer unit, the control part includes: a signal transceiving unit, a control unit and a signal processing unit.
[0048] The bracket is used to carry the transducer unit, and is adsorbed on the bottom of the steel box girder top plate 9 to be tested through the magnetic wheel set, so that the transducer unit can be close to or close to the bottom of the steel box girder top plate 9 to be tested, and can also drive The transducer unit moves along the length direction of the steel box girder U-shaped rib 10, the transducer unit includes at least one transducer 51, and the transducer 51 is used to excite the ultrasonic guided wave signal in t...
specific Embodiment approach 2
[0067] Specific implementation mode two: refer to Figure 4 , 6 , 7 and 8 specifically illustrate this embodiment. This embodiment is a further description of a fatigue crack detection system for orthotropic steel bridge deck roofs based on the ultrasonic guided wave method described in Embodiment 1. In this embodiment, The support includes a frame 1 and at least one transducer connecting rod 5, and the transducer connecting rod 5 has the same number as the transducer 51;
[0068] The frame 1 is provided with two groups of mirror-symmetric rod groups, each group of rod groups includes k wheel connecting rods parallel to each other and arranged along a straight line, k is a positive integer, and the free end of each wheel connecting rod is There is a magnetic wheel set, the transducer connecting rod 5 is fixed on the frame 1, and is parallel to the connecting rod of the wheel set, the free end of each wheel set connecting rod is sleeved with a rigid limiter 4, and the rigid li...
specific Embodiment approach 3
[0069] Specific embodiment three: This embodiment is a further description of a fatigue crack detection system based on the ultrasonic guided wave method described in the second specific embodiment, orthotropic steel bridge deck top plate fatigue crack detection system, in this embodiment, when k=2 The frame 1 includes at least one connecting beam 12 and two U-shaped frames 11, the two U-shaped frames 11 are mirror-symmetrically arranged, and the planes where they are located are parallel to each other, and the two U-shaped frames 11 are fixedly connected to each other through the connecting beam 12. The energy device connecting rod 5 is fixed on the connecting beam 12, and the bar at the free end of the U-shaped frame 11 is used as the wheel set connecting rod.
PUM
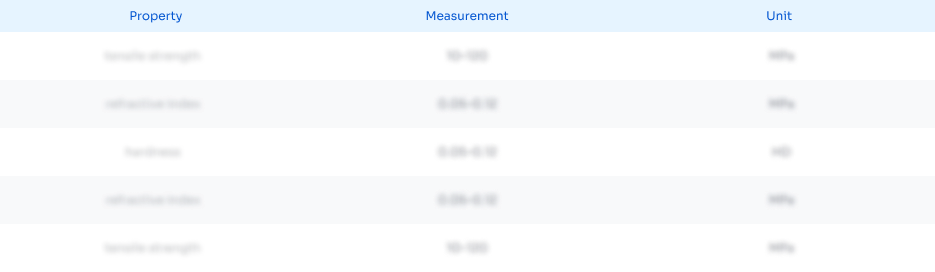
Abstract
Description
Claims
Application Information

- Generate Ideas
- Intellectual Property
- Life Sciences
- Materials
- Tech Scout
- Unparalleled Data Quality
- Higher Quality Content
- 60% Fewer Hallucinations
Browse by: Latest US Patents, China's latest patents, Technical Efficacy Thesaurus, Application Domain, Technology Topic, Popular Technical Reports.
© 2025 PatSnap. All rights reserved.Legal|Privacy policy|Modern Slavery Act Transparency Statement|Sitemap|About US| Contact US: help@patsnap.com