Waste heat recovery system of flue gas in power plant and recovery method thereof
A flue gas waste heat and recovery system technology, applied in the field of flue gas waste heat treatment, can solve the problem of low heat transfer coefficient of one-way fluid in water-cooled heat exchangers, which is difficult to adapt to boiler operation and coal type change factors, heat exchangers and water circulation Problems such as high system cost, to achieve the effect of cheap phase change point adjustment, avoiding flue gas dew point, and reducing system life
- Summary
- Abstract
- Description
- Claims
- Application Information
AI Technical Summary
Problems solved by technology
Method used
Image
Examples
Embodiment Construction
[0026] attached by figure 1 Shown: a flue gas waste heat recovery system in a power plant (the flue gas at the tail of the power plant is usually divided into two flues for discharge), the system includes: the first flue gas exchanger for heat exchange between the working medium (organic medium) Heater 1, second flue gas heat exchanger 2 for heat exchange between working fluid and flue gas, condensed water heat exchanger 3, heat network water heat exchanger 4 and liquid storage tank 5, the first flue gas exchanger The heater 1 is connected to the liquid storage tank 5 through the first working medium pipeline 6, and a first working medium pump 7 and a first valve 8 are arranged between the first working medium pipeline 6 and the liquid storage tank 5, and the second A second working fluid pump 10 and a second valve 11 are arranged between the working fluid pipeline 9 and the liquid storage tank 5; a first working fluid ( vapor-liquid mixture) pipeline 12, a third valve 13 is ...
PUM
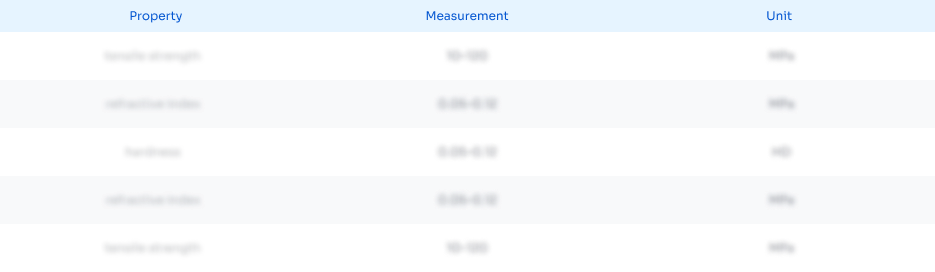
Abstract
Description
Claims
Application Information

- Generate Ideas
- Intellectual Property
- Life Sciences
- Materials
- Tech Scout
- Unparalleled Data Quality
- Higher Quality Content
- 60% Fewer Hallucinations
Browse by: Latest US Patents, China's latest patents, Technical Efficacy Thesaurus, Application Domain, Technology Topic, Popular Technical Reports.
© 2025 PatSnap. All rights reserved.Legal|Privacy policy|Modern Slavery Act Transparency Statement|Sitemap|About US| Contact US: help@patsnap.com