Preparation method of a wave-absorbing and radiation-proof composite textile material
A textile material and radiation protection technology, applied in shielding materials, textiles and papermaking, inorganic raw rayon, etc., can solve the problems of decreased textile performance of fabrics, difficult media loading, etc., to improve textile performance, reduce fiber spacing, The effect of increased ohmic loss
- Summary
- Abstract
- Description
- Claims
- Application Information
AI Technical Summary
Problems solved by technology
Method used
Image
Examples
Embodiment 1
[0052] In parts by weight, weigh 40 parts of polydimethylsilane and 100 parts of xylene respectively, place polydimethylsilane in the reaction kettle, feed high-purity nitrogen protection at an air flow rate of 40mL / min, and The heating rate of ℃ / min is raised to 200 ℃, kept for 20 minutes, and cooled to normal temperature to obtain the primary product of polycarbosilane. Add the primary product of polycarbosilane to xylene and stir at 300 r / min for 20 minutes at room temperature to obtain a mixed solution. Put the mixed solution under the conditions of pressure 300KPa and temperature 340°C to distill under reduced pressure 2, cool to room temperature to obtain polycarbosilane, put polycarbosilane in a melt spinning machine, and pass nitrogen gas at a gas flow rate of 40mL / min Protected, extruded under the conditions of pressure 0.2MPa and temperature 240°C, cooled to room temperature to obtain polycarbosilane fiber precursors, and placed polycarbosilane fiber precursors in a v...
Embodiment 2
[0054]In parts by weight, weigh 45 parts of polydimethylsilane and 110 parts of xylene respectively, place polydimethylsilane in the reaction kettle, feed high-purity nitrogen protection at an air velocity of 560mL / min, and The heating rate of ℃ / min is raised to 200 ℃, kept for 30 minutes, and cooled to normal temperature to obtain the primary product of polycarbosilane. Add the primary product of polycarbosilane to xylene, stir at 350 r / min at normal temperature for 25 minutes, and obtain a mixed solution. Put the mixed solution under the conditions of pressure 350KPa and temperature 350°C to distill under reduced pressure 3, cool to room temperature to obtain polycarbosilane, put the polycarbosilane in a melt-spinning machine, and pass nitrogen gas at a gas flow rate of 45mL / min Protected, extruded under the conditions of pressure 0.3MPa and temperature 250°C, cooled to room temperature to obtain polycarbosilane fiber precursors, and placed polycarbosilane fiber precursors in...
Embodiment 3
[0056] In parts by weight, weigh 50 parts of polydimethylsilane and 120 parts of xylene respectively, place polydimethylsilane in the reaction kettle, feed high-purity nitrogen protection at an air flow rate of 60mL / min, and The heating rate of ℃ / min is raised to 200 ℃, kept for 40 minutes, and cooled to normal temperature to obtain the primary product of polycarbosilane. Add the primary product of polycarbosilane to xylene and stir at 400 r / min for 30 minutes at room temperature to obtain a mixed solution. Distill the mixed solution under the conditions of pressure 400KPa and temperature 360°C under reduced pressure 4, cool to room temperature to obtain polycarbosilane, place polycarbosilane in a melt spinning machine, and pass nitrogen gas at a flow rate of 50mL / min Protected, extruded under the conditions of pressure 0.4MPa and temperature 260°C, and cooled to room temperature to obtain polycarbosilane fiber precursors. Place polycarbosilane fiber precursors in a vertical no...
PUM
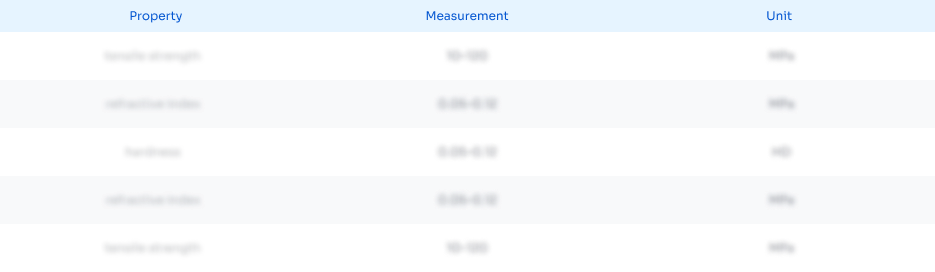
Abstract
Description
Claims
Application Information

- R&D
- Intellectual Property
- Life Sciences
- Materials
- Tech Scout
- Unparalleled Data Quality
- Higher Quality Content
- 60% Fewer Hallucinations
Browse by: Latest US Patents, China's latest patents, Technical Efficacy Thesaurus, Application Domain, Technology Topic, Popular Technical Reports.
© 2025 PatSnap. All rights reserved.Legal|Privacy policy|Modern Slavery Act Transparency Statement|Sitemap|About US| Contact US: help@patsnap.com