Test method of oxidation burning loss rate of billet steel processed by steel rolling heating furnace
A test method and billet technology, applied in the steel rolling heating furnace and metallurgy field, can solve the problems of organization implementation difficulties, inaccurate oxidation burning loss rate, inaccurate test, etc., to achieve a simple and easy test method, without affecting the production rhythm, simplifying The effect of the test step
- Summary
- Abstract
- Description
- Claims
- Application Information
AI Technical Summary
Problems solved by technology
Method used
Image
Examples
Embodiment
[0066] (1) Overview of production
[0067] U75V billet, the billet size is (length (B) × width (D) × height (H)) = 7680mm × 380mm × 280mm, and the mass is about 6.4t. The billet enters the furnace at 80°C and exits at 1201°C, staying in the heating furnace for 4.0h.
[0068] (2) Making steel samples
[0069] Take samples from the site and produce steel samples with a certain size (length (b) × width (d) × height (h)). In order to make the test more accurate, keep the size of the steel sample in proportion to the actual billet size during production, that is According to the convenience of actual operation, 3 steel samples with b×d×h=100mm×5mm×3.6mm were made.
[0070] (3) Making test modules
[0071] The base 101 is made, the size of the base is not strict, and the steel sample 2 can be placed steadily. Therefore, a base of length×width×thickness=250mm×150mm×(10-15)mm is made, the base is steel plate and its material is stainless steel. Weld on the base 101 such as figure 1 , figur...
PUM
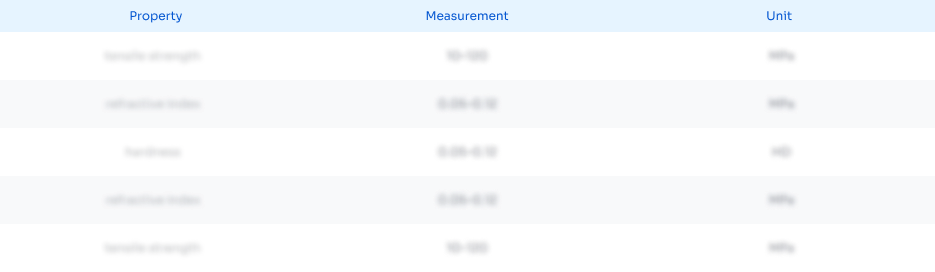
Abstract
Description
Claims
Application Information

- R&D Engineer
- R&D Manager
- IP Professional
- Industry Leading Data Capabilities
- Powerful AI technology
- Patent DNA Extraction
Browse by: Latest US Patents, China's latest patents, Technical Efficacy Thesaurus, Application Domain, Technology Topic, Popular Technical Reports.
© 2024 PatSnap. All rights reserved.Legal|Privacy policy|Modern Slavery Act Transparency Statement|Sitemap|About US| Contact US: help@patsnap.com