Method for avoiding in-furnace detonation in furnace shutdown process of 3200 m3 blast furnace
A technology for blast furnaces and blast furnaces, which is applied to the safe shutdown of blast furnaces, avoiding the knocking in the blast furnace during the shutdown of the 3200m3 blast furnace, and avoiding the knocking in the blast furnace, which can solve the problems of prolonging the gas recovery time, low safety and cost High-level problems, to achieve the effect of safe shutdown, low shutdown cost, and easy operation
- Summary
- Abstract
- Description
- Claims
- Application Information
AI Technical Summary
Problems solved by technology
Method used
Image
Examples
Embodiment 1
[0026] Embodiment 1, blast furnace volume is 3200m 3 , refer to figure 1 , an avoidance of 3200m 3 A method for generating knocking in a blast furnace during shutdown, comprising the following steps:
[0027]1) Complete the laying of the nitrogen pipeline 3 between the nitrogen pipeline 5 near the blast furnace and the furnace shaft coal injection hole 10 before the pre-shutdown of the blast furnace, and install a manual shut-off valve a 12, a pressure gauge a 14 and a nitrogen flow meter a 16 on the pipeline ,; Similarly, the nitrogen pipeline 4 laying between the nitrogen pipeline 5 near the blast furnace and the static pressure hole 11 of the furnace body is completed before the pre-shutdown of the blast furnace, and a manual shut-off valve b 13, a pressure gauge b 15 and a nitrogen flow meter are installed on the pipeline b 17; Complete the external laying between the nitrogen pipeline 3 and the coal injection hole 10, the external laying of the nitrogen pipeline 4 and t...
PUM
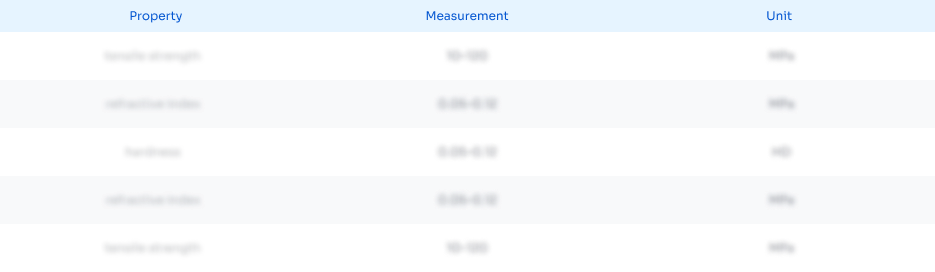
Abstract
Description
Claims
Application Information

- R&D
- Intellectual Property
- Life Sciences
- Materials
- Tech Scout
- Unparalleled Data Quality
- Higher Quality Content
- 60% Fewer Hallucinations
Browse by: Latest US Patents, China's latest patents, Technical Efficacy Thesaurus, Application Domain, Technology Topic, Popular Technical Reports.
© 2025 PatSnap. All rights reserved.Legal|Privacy policy|Modern Slavery Act Transparency Statement|Sitemap|About US| Contact US: help@patsnap.com