System and method for supplying heat to combined circulation machine group of last stage blades of cooling steam turbine
A technology of combined cycle unit and last-stage blades, which is applied in the direction of blade support elements, steam engine devices, combined combustion mitigation, etc., and can solve the problem of endangering the safe operation of the last-stage blades, the small amount of steam flowing through the final-stage blades, and the distributed energy capacity minor issues
- Summary
- Abstract
- Description
- Claims
- Application Information
AI Technical Summary
Problems solved by technology
Method used
Image
Examples
Embodiment Construction
[0032]In order to better understand the present invention, the present invention will be further described below in conjunction with accompanying drawing and specific embodiment:
[0033] Such as figure 1 As shown, a combined cycle heat supply system for cooling the final stage blades of a steam turbine includes a gas turbine generator set, a waste heat boiler 6, a steam turbine generator set, a low-pressure steam drum 31, a high-pressure steam drum 7, a condensate pump, a feed water pump, and pipelines ,valve;
[0034] The gas turbine generator set includes a gas turbine generator 1, an air compressor 2, and a gas turbine 5; the gas turbine generator 1, the air compressor 2, and the gas turbine 5 are connected in sequence; the air compressor 2, and the gas turbine 5 are respectively connected to the combustion chamber 4; The chamber 4 is connected with the gas pipeline through the fuel regulating valve 3;
[0035] The waste heat boiler 6 includes a condensate heater 32, a l...
PUM
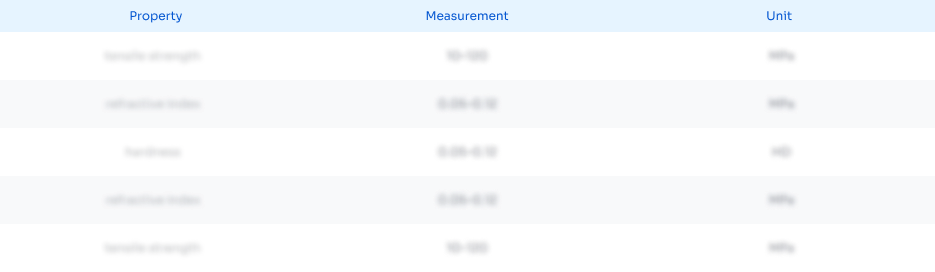
Abstract
Description
Claims
Application Information

- R&D
- Intellectual Property
- Life Sciences
- Materials
- Tech Scout
- Unparalleled Data Quality
- Higher Quality Content
- 60% Fewer Hallucinations
Browse by: Latest US Patents, China's latest patents, Technical Efficacy Thesaurus, Application Domain, Technology Topic, Popular Technical Reports.
© 2025 PatSnap. All rights reserved.Legal|Privacy policy|Modern Slavery Act Transparency Statement|Sitemap|About US| Contact US: help@patsnap.com