A Textile Fiber Press Forming Machine Using the Principle of Displaced Flat Carding
A textile fiber and forming machine technology, applied in the direction of material forming presses, presses, manufacturing tools, etc., can solve the problems of lack of screening function, inability to guarantee uniformity, large deformation of fiber materials, etc., to prevent uniformity The degree of influence is affected, the deformation is avoided, and the effect of the drag force is increased.
- Summary
- Abstract
- Description
- Claims
- Application Information
AI Technical Summary
Problems solved by technology
Method used
Image
Examples
Embodiment
[0028] see Figure 1-Figure 6 , the present invention provides a textile fiber press molding machine using the principle of dislocation flat combing, the structure of which includes a servo cabinet Q1, an inspection door Q2, a processing table Q3, a heat sink Q4, a host machine Q5, a fixed foot Q6, a locker Q7, Controller Q8, the controller Q8 is installed on the top of the locker Q7 by embedding, the back of the locker Q7 is buckled and connected with the right end of the surface of the main machine Q5, and the processing table Q3 is set on the top of the main machine Q5 and integrated The servo cabinet Q1 has a rectangular structure, and the bottom is installed on the left end of the processing table Q3 by buckling. The left side of the main machine Q5 is provided with a cooling groove Q4, which is an integrated structure. There are four, and they are installed on the four ends of the bottom of the main machine Q5 by buckling. The left side of the maintenance door Q2 is hing...
PUM
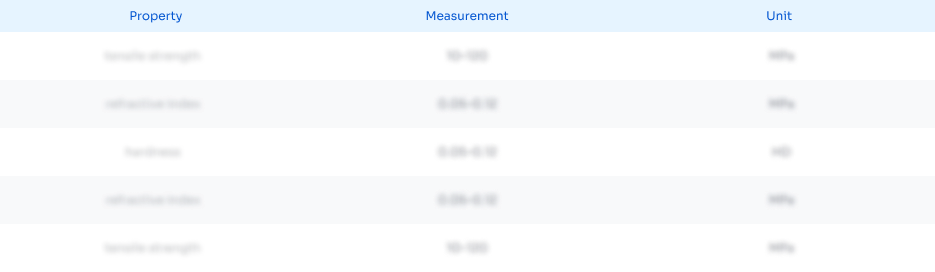
Abstract
Description
Claims
Application Information

- R&D
- Intellectual Property
- Life Sciences
- Materials
- Tech Scout
- Unparalleled Data Quality
- Higher Quality Content
- 60% Fewer Hallucinations
Browse by: Latest US Patents, China's latest patents, Technical Efficacy Thesaurus, Application Domain, Technology Topic, Popular Technical Reports.
© 2025 PatSnap. All rights reserved.Legal|Privacy policy|Modern Slavery Act Transparency Statement|Sitemap|About US| Contact US: help@patsnap.com