Injection mold structure suitable for forming power battery relay shell blank body
A power battery and injection mold technology, applied in the field of injection molds, can solve the problems of large product deformation, increased process, and large internal stress of the molding body, so as to improve product performance and yield, reduce air holes and cracks, and enhance sealing performance. Effect
- Summary
- Abstract
- Description
- Claims
- Application Information
AI Technical Summary
Problems solved by technology
Method used
Image
Examples
Embodiment 1
[0020] Such as figure 1 As shown, an injection mold structure suitable for forming a power battery relay shell blank body includes a hot runner nozzle 1, a nozzle 6, an injection molded part 2, an action cylinder 3, an injection machine ejector rod 9, and a cutting push plate 4, The nozzle needle push plate 7, the cutting needle 5, and the nozzle needle 8, the hot runner nozzle 1 and the nozzle 6 are fixed on the upper end of the injection molded part 2, and the nozzle needle 8 and the material cutting needle 5 are fixed below the injection molded part 2, The material cutting needle 5 is connected with the material cutting push plate 4, the nozzle needle 8 is connected with the water outlet needle push plate 7, the action cylinder 3 is fixed on the material cutting push plate 4, and the ejector rod 9 of the injection machine is fixed on On the nozzle needle push plate 7. The ceramic rubber enters the cavity of the injection molded part from the hot runner nozzle 1 to complete...
PUM
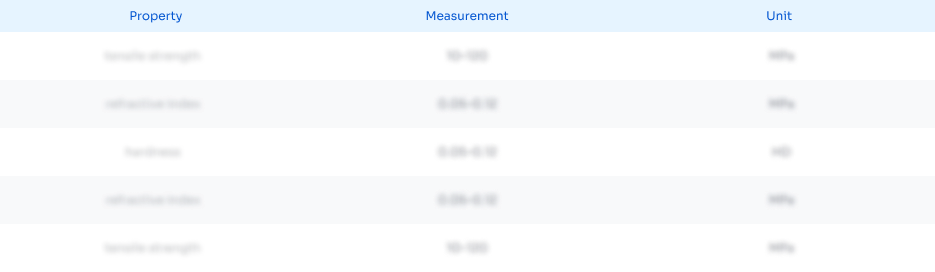
Abstract
Description
Claims
Application Information

- R&D
- Intellectual Property
- Life Sciences
- Materials
- Tech Scout
- Unparalleled Data Quality
- Higher Quality Content
- 60% Fewer Hallucinations
Browse by: Latest US Patents, China's latest patents, Technical Efficacy Thesaurus, Application Domain, Technology Topic, Popular Technical Reports.
© 2025 PatSnap. All rights reserved.Legal|Privacy policy|Modern Slavery Act Transparency Statement|Sitemap|About US| Contact US: help@patsnap.com