Waterproof type heat-insulating mortar and construction process thereof
A technology of thermal insulation mortar and construction technology, which is applied to other household appliances, household appliances, applications, etc., can solve the problem of high phase transition temperature, and achieve the effect of improving elastic strain performance and improving deformation.
- Summary
- Abstract
- Description
- Claims
- Application Information
AI Technical Summary
Problems solved by technology
Method used
Examples
Embodiment 1
[0025] The specific preparation process of the phase-change diatomite powder is as follows: 10g of myristyl alcohol and 22g of lauric acid are added to the stirring tank at the same time, the temperature in the stirring tank is controlled to be 10-15°C, and 5.3g of diatomite is added to it at the same time, and then the Vacuumize the stirred tank for 20-30min, then slowly raise the temperature to 50°C, control the heating rate to 1°C / min, heat it up to 50°C and keep it warm for 60-70min, then filter while it is hot, and then quickly put the solid into the 0-5°C Cool in the freezer, then add 10g of liquid phenolic resin and 2.3g of hexamethylenetetramine into the reaction vessel simultaneously, add 4.5g of the cooled solid thereinto at the same time, stir and mix at room temperature for 4-6min, then filter, and Dry and solidify the filtered solid at room temperature to obtain phase-change diatomite powder.
Embodiment 2
[0027] The specific preparation process of the phase-change diatomite powder is as follows: 10g of myristyl alcohol and 22g of lauric acid are added to the stirring tank at the same time, the temperature in the stirring tank is controlled to be 10-15°C, and 5.3g of diatomite is added to it at the same time, and then the Vacuumize the stirred tank for 20-30min, then slowly raise the temperature to 50°C, control the heating rate to 1°C / min, heat it up to 50°C and keep it warm for 60-70min, then filter while it is hot, and then quickly put the solid into the 0-5°C Cool in a freezer to obtain a phase-change diatomite powder.
Embodiment 3
[0029] The specific preparation process of the joint filler is as follows:
[0030] Step 1: Add urea and 2,5-dihydroxybenzaldehyde into the reaction vessel at a ratio of 1:2, and add water to the reaction vessel at the same time, then raise the temperature to 50°C and stir for 4 hours, then raise the temperature To 75°C, add isopropyl titanate into the reaction vessel, the amount of isopropyl titanate added is half of the amount of urea, stir and react for 3-4h, then filter, wash and dry to obtain tetraphenolic hydroxyl Titanate;
[0031] Step 2: Then add 10g of dried tetraphenol hydroxy titanate into 150mL of 1% dilute hydrochloric acid solution, add 13g of ethanedithiol to it at the same time, and then heat up to 80-85°C for reflux reaction for 20-22h , and then carry out vacuum distillation, and wash the obtained product to neutrality and then dry to obtain titanium phenol monomer;
[0032] Step 3: Add 10 g of the titanium phenolic monomer obtained in Step 2 into 120 mL o...
PUM
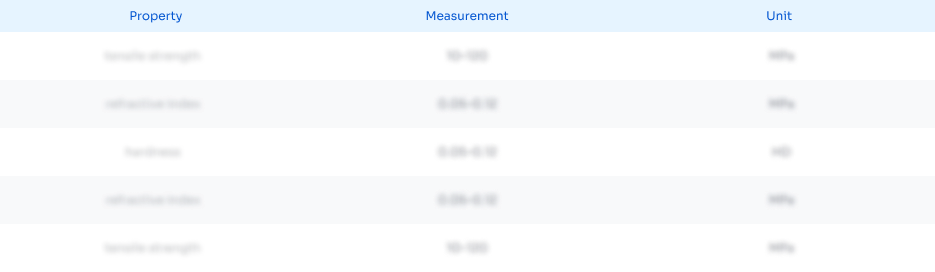
Abstract
Description
Claims
Application Information

- R&D
- Intellectual Property
- Life Sciences
- Materials
- Tech Scout
- Unparalleled Data Quality
- Higher Quality Content
- 60% Fewer Hallucinations
Browse by: Latest US Patents, China's latest patents, Technical Efficacy Thesaurus, Application Domain, Technology Topic, Popular Technical Reports.
© 2025 PatSnap. All rights reserved.Legal|Privacy policy|Modern Slavery Act Transparency Statement|Sitemap|About US| Contact US: help@patsnap.com