Combining force control search assembly method
An assembly method and flexible assembly technology, applied in the direction of assembly machines, metal processing equipment, manufacturing tools, etc., can solve the problems of poor machining accuracy, affecting the production process, not satisfying automation, etc., to improve dynamic characteristics, improve assembly success rate, Improve the effect of dynamic response characteristics
- Summary
- Abstract
- Description
- Claims
- Application Information
AI Technical Summary
Problems solved by technology
Method used
Image
Examples
Embodiment Construction
[0058] Embodiments of the present invention are described in detail below, examples of which are shown in the drawings, wherein the same or similar reference numerals designate the same or similar elements or elements having the same or similar functions throughout. The embodiments described below by referring to the figures are exemplary and are intended to explain the present invention and should not be construed as limiting the present invention.
[0059] Such as figure 1 As shown, the search and assembly method combined with force control in the embodiment of the present invention includes the following steps:
[0060] Step S1, build a flexible assembly platform based on the collaborative robot, combined with force control and search algorithms. Such as figure 2 As shown, the flexible assembly platform includes: a collaborative robot body 1, a collaborative robot controller 5, a host computer 6, an end effector 2, an assembly workpiece axis 3, and an assembly workpiece ...
PUM
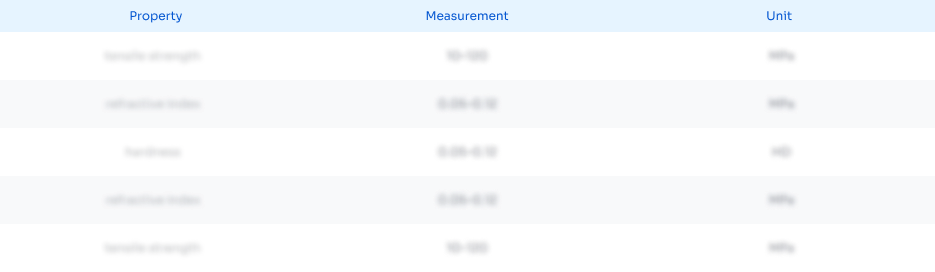
Abstract
Description
Claims
Application Information

- R&D
- Intellectual Property
- Life Sciences
- Materials
- Tech Scout
- Unparalleled Data Quality
- Higher Quality Content
- 60% Fewer Hallucinations
Browse by: Latest US Patents, China's latest patents, Technical Efficacy Thesaurus, Application Domain, Technology Topic, Popular Technical Reports.
© 2025 PatSnap. All rights reserved.Legal|Privacy policy|Modern Slavery Act Transparency Statement|Sitemap|About US| Contact US: help@patsnap.com