A New Process for the Production of Sheets by Rolling
A thin sheet production and new process technology, applied in tobacco, tobacco processing, tobacco preparation, etc., can solve the problems of unsatisfactory effect and insufficient persistence of tobacco flavor release, so as to increase the use value, improve the internal sensory quality, and reduce production costs Effect
- Summary
- Abstract
- Description
- Claims
- Application Information
AI Technical Summary
Problems solved by technology
Method used
Image
Examples
Embodiment 1
[0022] Get the flue-cured tobacco leaves K in a certain production area in the warehouse of the company, and prepare thin slice raw materials according to the process of the present invention. The specific steps are as follows: Dry the flue-cured tobacco leaves K at 80°C at a low temperature until the water content reaches 10%, weigh 20kg of flue-cured tobacco leaves K, and pulverize them with a pulverizer. hour, then dried and concentrated into a material with a water content of about 20%, and then sent to a constant temperature reactor at 80°C, and 120.0g of amino acid A (0.6% of the dry material weight) and 6.0kg of non-aqueous reaction medium were added in the reactor G (30.0% of the dry material weight), adding a pH regulator to adjust the pH to 8-9, reacting and fermenting for 3 hours, and stirring, the stirring speed is 15 rpm, then quantitatively transported to a high-speed mixer, while adding 5.0% adhesive, 2.0% of the dispersed fibers were homogenized at high speed, ...
Embodiment 2
[0024] Take waste tobacco powder M from the workshop of the company's tobacco factory, and prepare flake raw materials according to the process of the present invention. The specific steps are as follows: Dry the waste tobacco powder M at a low temperature of 80°C until the water content is 10%, weigh 20kg of waste tobacco powder M, and then pulverize it with a pulverizer. Extracted for 2 hours, then dried and concentrated into a material with a water content of about 20%, and then sent to a constant temperature reactor at 90°C, 160.0g of amino acid A (0.8% of the dry material weight) and 8.0kg of non-aqueous Reaction medium G (40.0% of the dry material weight), adding a pH regulator to adjust the pH to 8-9, reacting and fermenting for 5 hours, and stirring at a stirring speed of 15 rpm, then quantitatively transported to a high-speed mixer, while adding 5.0% Adhesive, 2.0% dispersed fibers, after high-speed mixing, tablet forming, low-temperature drying at 80°C, shredding, an...
Embodiment 3
[0026] Tobacco stem Y is taken from the company's warehouse, and thin slice raw material preparation is carried out according to the process of the present invention. The specific steps are as follows: Dry the tobacco stem Y at a low temperature of 80°C until the water content reaches 10%, weigh 20kg of the tobacco stem Y, and then pulverize it with a pulverizer. hour, then dried and concentrated into a material with a water content of about 20%, and then sent to a constant temperature reactor at 100°C, in the reactor, 2000.0g amino acid A (10.0% of the dry material weight), 16.0kg of non-aqueous reaction medium were added G (80.0% of the weight of the dry material) and 1250.0g glucose, add a pH regulator to adjust the pH to 8-9, react and ferment for 9 hours, and stir, the stirring speed is 15 rpm, then quantitatively transported to a high-speed mixer, and add 5.0% adhesive, 2.0% dispersed fiber, after high-speed mixing, tablet molding, low-temperature drying at 80°C, cutting...
PUM
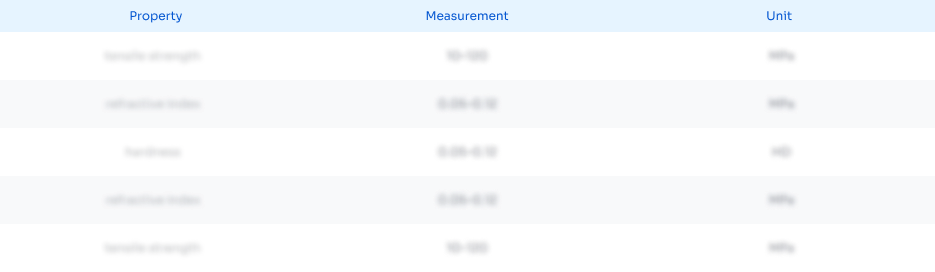
Abstract
Description
Claims
Application Information

- R&D Engineer
- R&D Manager
- IP Professional
- Industry Leading Data Capabilities
- Powerful AI technology
- Patent DNA Extraction
Browse by: Latest US Patents, China's latest patents, Technical Efficacy Thesaurus, Application Domain, Technology Topic, Popular Technical Reports.
© 2024 PatSnap. All rights reserved.Legal|Privacy policy|Modern Slavery Act Transparency Statement|Sitemap|About US| Contact US: help@patsnap.com