Graphite-like phase carbon nitride coated [alpha]-Fe2O3 material, and preparation and application thereof
A graphite phase carbon nitride and coating technology, which is applied in the direction of electrochemical generators, active material electrodes, electrical components, etc., can solve the problems of low initial Coulombic efficiency, volume expansion during charging and discharging, and difficulty in meeting future needs. Achieve the effects of thin and uniform coating layer, enhanced electrical conductivity, and stable cycle performance
- Summary
- Abstract
- Description
- Claims
- Application Information
AI Technical Summary
Problems solved by technology
Method used
Image
Examples
Embodiment 1
[0031] A Kind of Graphite Phase Carbon Nitride Coated α-Fe 2 o 3 The preparation method of the material comprises the following steps: adding 0.01 mol of ferric nitrate to 200 ml of deionized water to dissolve, then adding 0.05 mol of urea, stirring for 1 hour by magnetic force, and dispersing by ultrasonic wave for 0.5 hours to obtain a precursor solution; taking the precursor solution in a tube furnace In an air atmosphere, heat up to 200°C at a rate of 3°C / min, sinter for 2 hours, then heat up to 400°C at a rate of 3°C / min, and sinter for 2 hours, then take it out and wash it alternately with deionized water for 3 times to medium properties, vacuum drying at 80°C for 24 hours to obtain graphite-like carbon nitride-coated α-Fe 2 o 3 Material.
Embodiment 2
[0033] A Kind of Graphite Phase Carbon Nitride Coated α-Fe 2 o 3 The preparation method of the material comprises the following steps: adding 0.01 mol of ferric nitrate to 200 ml of deionized water to dissolve, then adding 0.05 mol of urea, stirring for 1 hour by magnetic force, and dispersing by ultrasonic wave for 0.5 hours to obtain a precursor solution; taking the precursor solution in a tube furnace In an air atmosphere, heat up to 300°C at a rate of 3°C / min, sinter for 2 hours, then heat up to 600°C at a rate of 3°C / min, sinter for 2 hours, then take out and wash with deionized water alternately 3 times to medium properties, vacuum drying at 80°C for 24 hours to obtain graphite-like carbon nitride-coated α-Fe 2 o 3 Material.
Embodiment 3
[0035] A Kind of Graphite Phase Carbon Nitride Coated α-Fe 2 o 3 The preparation method of the material comprises the following steps: adding 0.01 mol of ferric nitrate to 200 ml of deionized water to dissolve, then adding 0.1 mol of urea, stirring for 1 hour by magnetic force, and dispersing by ultrasonic wave for 0.5 hours to obtain a precursor solution; taking the precursor solution in a tube furnace In an air atmosphere, heat up to 200°C at a rate of 3°C / min, sinter for 2 hours, then heat up to 600°C at a rate of 3°C / min, and sinter for 2 hours, then take it out and wash it alternately with deionized water for 3 times to medium properties, vacuum drying at 80°C for 24 hours to obtain graphite-like carbon nitride-coated α-Fe 2 o 3 Material.
PUM
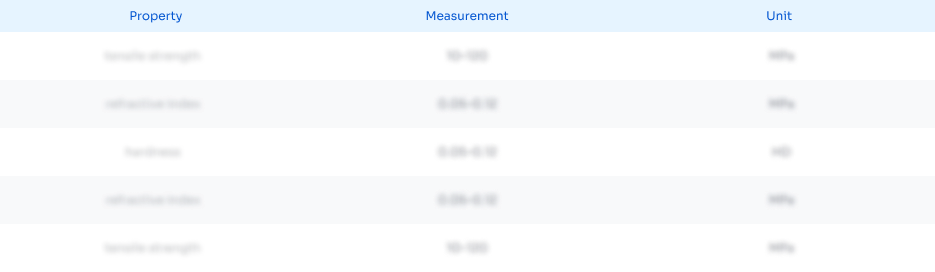
Abstract
Description
Claims
Application Information

- R&D Engineer
- R&D Manager
- IP Professional
- Industry Leading Data Capabilities
- Powerful AI technology
- Patent DNA Extraction
Browse by: Latest US Patents, China's latest patents, Technical Efficacy Thesaurus, Application Domain, Technology Topic, Popular Technical Reports.
© 2024 PatSnap. All rights reserved.Legal|Privacy policy|Modern Slavery Act Transparency Statement|Sitemap|About US| Contact US: help@patsnap.com