Low-odor rubber sealing material and preparation method thereof
A rubber sealing, low odor technology, applied in the field of automobile door sealing, can solve the problems of high cost, cumbersome process, unstable adsorption performance, etc., and achieve the effects of improving production efficiency, low overall cost, and fast material turnover.
- Summary
- Abstract
- Description
- Claims
- Application Information
AI Technical Summary
Problems solved by technology
Method used
Image
Examples
preparation example Construction
[0043] The application also provides a method for preparing the low-odor rubber sealing material, comprising the steps of:
[0044] (1) The first stage of mixing. Specifically:
[0045] First, add 100 parts of EPDM rubber, 5-7 parts of zinc oxide and 1-2 parts of stearic acid into the internal mixer, and banbury at a temperature of 60-80°C for 40-60 seconds. Preferably, at the end of this banburying, the top bolt is lifted up, in order to discharge the small molecular substances carried in the raw materials.
[0046] Then, continue to add 60-90 parts of fast extrusion carbon black, 30-60 parts of semi-reinforced carbon black, 70-100 parts of white calcium carbonate and 50-80 parts of paraffin oil in the internal mixer, and mix until 150- Discharging at 165°C. Preferably, the top bolt is lifted 1-2 times in the middle to volatilize some small molecular organic compounds.
[0047] Then, thin pass on the open mill, filter on the rubber filter, and release the sheet from the o...
Embodiment 1
[0057] First, weigh 100 parts of EPDM rubber, 65 parts of fast extrusion carbon black, 60 parts of semi-reinforcing carbon black, 80 parts of white material calcium carbonate, 65 parts of paraffin oil, 7 parts of zinc oxide, and 1.5 parts of stearic acid , 3 parts of polyethylene glycol, 5 parts of accelerator Perlorax ZET / S, 2.5 parts of accelerator CLD-80, 2 parts of sulfur, and 8 parts of hygroscopic agent. The white material calcium carbonate has not been activated beforehand.
[0058] Next, add EPDM rubber, zinc oxide and stearic acid into the internal mixer at a temperature of 60-80°C and internally knead for 40-60 seconds. Next, add carbon black, white material and paraffin oil into the internal mixer, and mix to 155-165°C to obtain the rubber compound; Small molecule organics exit the mixer. Subsequently, it is thinly passed on the mill, filtered with a rubber filter, and the sheet is released from the mill. At this time, the rubber compound was cooled to room tempe...
Embodiment 2
[0063] First, weigh 100 parts of EPDM rubber, 75 parts of fast extrusion carbon black, 50 parts of semi-reinforcing carbon black, 75 parts of white material calcium carbonate, 70 parts of paraffin oil, 6 parts of zinc oxide, and 1 part of stearic acid , 2 parts of polyethylene glycol, 4.5 parts of accelerator Perlorax ZET / S, 3 parts of accelerator CLD-80, 1.5 parts of sulfur, and 8 parts of hygroscopic agent.
[0064] Next, add EPDM rubber, zinc oxide and stearic acid into the internal mixer at a temperature of 60-80°C and internally knead for 40-60 seconds. Next, add carbon black, white material and paraffin oil into the internal mixer, and knead to 155-165°C to obtain the rubber compound; preferably, the small molecular organic matter generated during the mixing process is discharged from the internal mixer 1- 2 times. Subsequently, it is thinly passed on the mill, filtered with a rubber filter, and the sheet is released from the mill. At this time, the rubber compound was...
PUM
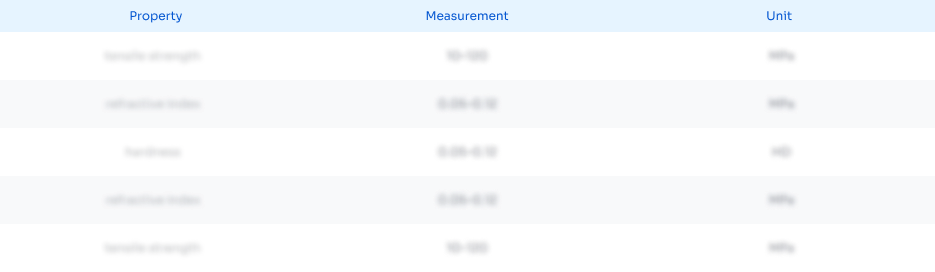
Abstract
Description
Claims
Application Information

- Generate Ideas
- Intellectual Property
- Life Sciences
- Materials
- Tech Scout
- Unparalleled Data Quality
- Higher Quality Content
- 60% Fewer Hallucinations
Browse by: Latest US Patents, China's latest patents, Technical Efficacy Thesaurus, Application Domain, Technology Topic, Popular Technical Reports.
© 2025 PatSnap. All rights reserved.Legal|Privacy policy|Modern Slavery Act Transparency Statement|Sitemap|About US| Contact US: help@patsnap.com