Hole inner wall wear-resistant layer preparation method capable of increasing product percent of pass
A technology of product pass rate and wear-resistant layer, which is applied in the field of nuclear power plant control rod drive mechanism parts manufacturing, can solve problems such as low pass rate, achieve the effects of improving product pass rate, realizing batch production, and benefiting welding quality
- Summary
- Abstract
- Description
- Claims
- Application Information
AI Technical Summary
Problems solved by technology
Method used
Image
Examples
Embodiment 1
[0043] Such as Figure 3 to Figure 7 As shown, a method for preparing the wear-resistant layer on the inner wall of the hole that can improve the product qualification rate is used to obtain a wear-resistant layer on the surface of the prefabricated hole 6 of the part 5, and finally obtain a wear-resistant layer on the part 5 with an inner diameter of D and a wear-resistant hole wall. Layer holes, including the following steps:
[0044] S1. Drill a prefabricated hole 6 with an inner diameter of D1 on the part 5, where D1>D; obtain a filler rod 1 for welding, the outer diameter of the filler rod 1 is smaller than D1 and larger than D;
[0045] S2. Insert the filling mandrel 1 into the prefabricated hole 6, and fill the gap 7 between the filling mandrel 1 and the prefabricated hole 6 by filling welding or self-fusion welding;
[0046] S3. A hole with a diameter of D is obtained on the filling mandrel 1, and the filling mandrel 1 provides all hole walls for the hole with a diame...
Embodiment 2
[0054] This embodiment is further limited on the basis of Embodiment 1. As a specific implementation, it is set as follows: the filling mandrel 1 is a hollow rod with a central hole;
[0055] The outer diameter D2 of the filling mandrel 1 satisfies the following relationship: D1>D2>D, the central hole diameter D3 is: D3≤D, and the material of the filling mandrel 1 is consistent with that of the wear-resistant layer. In this solution, the filling mandrel 1 is arranged in a tubular shape, the filling mandrel 1 is inserted into the prefabricated hole 6 and filled and welded, and then the final hole is obtained on the filling mandrel 1 . Adopting this scheme facilitates the final hole processing.
Embodiment 3
[0057] The present embodiment is further limited on the basis of Embodiment 1. As mentioned above, since the filling mandrel 1 needs to be filled and welded after being embedded in the prefabricated hole 6, in order to eliminate the surface layer of the center hole of the filling mandrel 1 to facilitate the quality of the hole wall, It is set as follows: said D3<D, and in step S3, said obtaining a hole with a diameter of D is: performing a hole reaming process on said central hole to obtain said hole with a diameter of D.
PUM
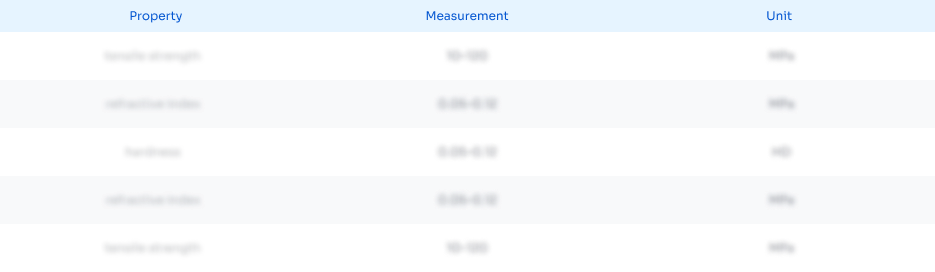
Abstract
Description
Claims
Application Information

- R&D
- Intellectual Property
- Life Sciences
- Materials
- Tech Scout
- Unparalleled Data Quality
- Higher Quality Content
- 60% Fewer Hallucinations
Browse by: Latest US Patents, China's latest patents, Technical Efficacy Thesaurus, Application Domain, Technology Topic, Popular Technical Reports.
© 2025 PatSnap. All rights reserved.Legal|Privacy policy|Modern Slavery Act Transparency Statement|Sitemap|About US| Contact US: help@patsnap.com