Flow diversion method for aluminum ingot turning and melting furnace
A technology for melting furnaces and aluminum ingots, applied in furnaces, crucible furnaces, furnace types, etc., can solve problems such as splashing, no filter residue function, and inability to pour out molten liquid, and achieve the effect of ensuring airtightness
- Summary
- Abstract
- Description
- Claims
- Application Information
AI Technical Summary
Problems solved by technology
Method used
Image
Examples
Embodiment
[0047] Such as Figure 1-10 As shown, the diversion method of the present invention for aluminum ingot turning and melting furnace is characterized in that it comprises steps:
[0048] Step 1. Set the furnace mouth sealing plate 1 to cover the molten liquid on the furnace mouth 7 of the turning melting furnace 6, and pour out the side. On the guide hole 8 on the inner surface of the furnace mouth sealing plate 1;
[0049] Step 2, setting the first diversion pipe 3 includes a sealing plate pipe section 9, a first diversion pipe section 10 and a first connecting pipe section 11, one end of the sealing plate pipe section 9 is vertically connected to the upper end of the first diversion pipe section 10; A connecting pipe section 11 is perpendicular to the sealing plate pipe section 9 and the first diversion pipe section 10, and is vertically connected with the lower end of the first diversion pipe section 10; the other end of the sealing plate pipe section 9 is provided with a fi...
PUM
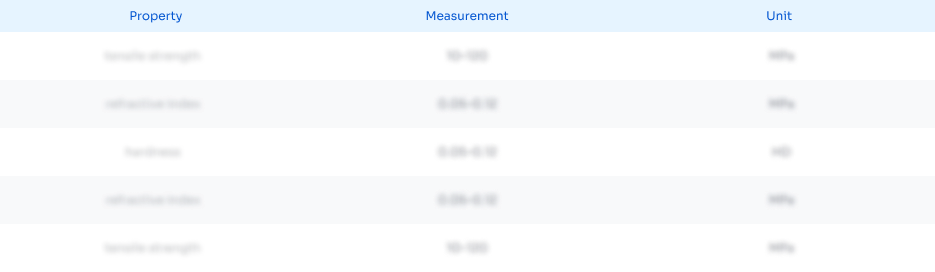
Abstract
Description
Claims
Application Information

- Generate Ideas
- Intellectual Property
- Life Sciences
- Materials
- Tech Scout
- Unparalleled Data Quality
- Higher Quality Content
- 60% Fewer Hallucinations
Browse by: Latest US Patents, China's latest patents, Technical Efficacy Thesaurus, Application Domain, Technology Topic, Popular Technical Reports.
© 2025 PatSnap. All rights reserved.Legal|Privacy policy|Modern Slavery Act Transparency Statement|Sitemap|About US| Contact US: help@patsnap.com