Preparation method for interfacial polymerization composite membrane
A technology of interfacial polymerization and composite membranes, applied in chemical instruments and methods, membrane technology, semipermeable membrane separation, etc., can solve problems such as difficulty in achieving high-performance separation membranes, difficulty in expanding production scale, time-consuming steps, etc., to achieve Good industrial applicability, low cost of raw materials, effect of increased performance
- Summary
- Abstract
- Description
- Claims
- Application Information
AI Technical Summary
Problems solved by technology
Method used
Examples
Embodiment 1
[0027] A preparation method of an interfacial polymerization composite membrane, the steps are as follows:
[0028] (1) Dissolve 7.5 g of polyethersulfone and 0.2 g of piperazine in 42.3 g of dimethyl sulfoxide solvent, and stir overnight to obtain a polyethersulfone casting solution with a concentration of 15 wt%.
[0029] (2) Let the prepared casting solution stand for defoaming, and then apply it on the non-woven fabric by an automatic scraper machine, the thickness of the scraper is 250 μm, and then immerse the non-woven fabric coated with the polymer solution in deionized water , take out the polyethersulfone membrane after 2min phase inversion;
[0030] (3) Use filter paper to remove the remaining liquid on the surface of the membrane, then immerse the membrane in a 0.04 wt% trimesoyl chloride-n-hexane solution for 1 min, and then treat it in an oven at 40°C for 10 min to obtain a composite nanofiltration membrane.
[0031] Separation membrane performance test:
[0032...
Embodiment 2
[0038] A preparation method of an interfacial polymerization composite membrane, the steps are as follows:
[0039] (1) Weighing 7.5 g of polyethersulfone and 2 g of piperazine were dissolved in 42.3 g of dimethylformamide solvent, and stirred overnight to obtain a polyethersulfone casting solution with a concentration of 15 wt%.
[0040] (2) Let the prepared casting solution stand for defoaming, and then apply it on the non-woven fabric by an automatic scraper machine, the thickness of the scraper is 250 μm, and then immerse the non-woven fabric coated with the polymer solution in deionized water , take out the polyethersulfone membrane after 30min phase inversion;
[0041] (3) Use filter paper to remove the remaining liquid on the surface of the membrane, then immerse the membrane in a 4 wt% trimesoyl chloride-n-hexane solution for 30 seconds, and then treat it in an oven at 40°C for 10 minutes to obtain a composite nanofiltration membrane.
[0042] The composite membrane f...
Embodiment 3
[0047] A preparation method of an interfacial polymerization composite membrane, the steps are as follows:
[0048] (1) Dissolve 8 g of polysulfone and 0.4 g of piperazine in 41.6 g of N-methylpyrrolidone and stir overnight to obtain a polysulfone casting solution with a concentration of 16 wt% containing piperazine monomer;
[0049] (2) Leave the prepared casting solution to stand for defoaming, and then apply it on the non-woven fabric by an automatic scraper machine, the thickness of the scraper is 250 μm, and then immerse the non-woven fabric coated with the polymer solution into the deionized aqueous solution In the process, take out the polysulfone membrane after 2min phase inversion;
[0050] (3) Use filter paper to remove the remaining liquid on the surface of the membrane, then immerse the membrane in a 0.2 wt% trimesoyl chloride-n-hexane solution for 1 min, and then treat it in an oven at 90°C for 1 min to obtain a composite nanofiltration membrane.
[0051] The pre...
PUM
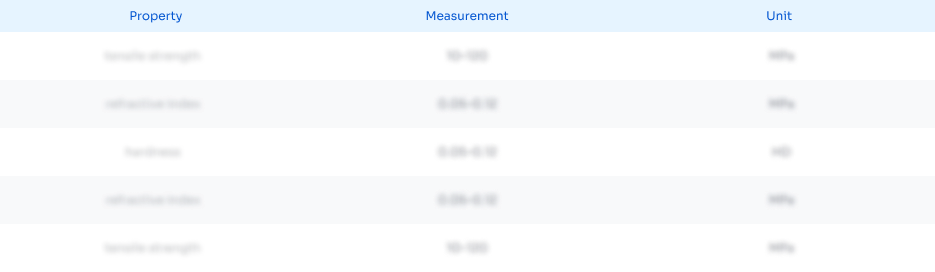
Abstract
Description
Claims
Application Information

- R&D
- Intellectual Property
- Life Sciences
- Materials
- Tech Scout
- Unparalleled Data Quality
- Higher Quality Content
- 60% Fewer Hallucinations
Browse by: Latest US Patents, China's latest patents, Technical Efficacy Thesaurus, Application Domain, Technology Topic, Popular Technical Reports.
© 2025 PatSnap. All rights reserved.Legal|Privacy policy|Modern Slavery Act Transparency Statement|Sitemap|About US| Contact US: help@patsnap.com